Подземный рудник
Подземный рудник: сложное горнодобывающее производство, с глубиной разведанных запасов руды в 1600 метров. Система разработки – этажно-камерная с закладкой выработанного пространства твердеющими смесями. Размеры камер: высота – 80 м., ширина – 20 м., длина камеры зависит от мощности рудного тела и меняется в пределах 70-80 м.
В настоящее время отработка Гайского месторождения ведется в этажах 750-830, 830-910, 910-990 и 990-1070м
На подземном руднике трудится более 2000 человек. В структуре подразделения — 21 производственный участок, геологоразведочная партия и 8 отделов. Деятельность одиннадцати участков связана непосредственно с подготовкой, добычей, транспортировкой руды и заполнением образованных пустот твердеющей закладкой.
О росте мощностей по годовой добыче руды за 55 лет существования подземного рудника говорят цифры: в 1960 году подземным способом было добыто 44 тысячи тонн руды. В 2016 году – 6,5 млн. тонн руды.
План 2017 года — добыть 7,5 миллиона тонн
Техническая оснащенность:
Под увеличение объемов по добыче руды Гайский ГОК активно обновляет парк горно-шахтного оборудования, горной самоходной техники. Выбор техники основывается на высоких стандартах в области безопасности, надежности и производительности. В настоящее время на службе у гайских горняков задействованы машины ведущих зарубежных и отечественных фирм, таких как: «Sandvik Mining and Construction Finland Corp» и «Normet» (Финляндия), «Caterpillar» (США), «Atlas Copco” (Швеция), «Zanam» (Польша), ООО «Хенкон Сибирь» (Россия, г. Красноярск).
В частности, доставка горной массы осуществляется самосвалами МТ 436В, CAT AD30, ТН 540, ТН-430 и погрузочно-доставочными машинами LH 410, LH 514, ST 1030 , LKP-1601M и САТ R1700G;
самосвал ТН-430
— бурение скважин в камерах осуществляется самоходными буровыми установками Sandvik DL410-15 и Simba M4C и БП-100С.;
— бурение шпуров осуществляется буровыми каретками Sandvik-DD 311-40, Boomer S1D.;
буровая каретка Boomer S1D
— проходка восстающих ведется комплексами КПН-4А, Robbins 73RH. . Проходка восстающих бурением позволяет значительно повысить безопасность работ, увеличить скорость проходки, с большой точностью выдержать сечение и направление выработки. Внедрение «безлюдных» способов проходки восстающих является исключительно важной задачей для совершенствования горных работ вообще и проходки восстающих выработок в частности.
— проветривание камер производится вентиляторами местного проветривания ВМЭ-12А;
— разделка негабаритных кусков горной массы в подземных условиях – самоходная машина LK-1 SWW1/1Н;
— крепление выработок торкретбетоном – ALIVA-252; Spraymec MF 050 VC
— доставка материалов и оборудования осуществляется – машинами SWT-3S, Hencon Transvers Mixer;
— обеспечение дизельным топливом технологического оборудования под землей – топливозаправщик SWT-07P.
Руда из камер глубоких горизонтов самоходным транспортом доставляется к капитальным рудоспускам, по которым она попадает в участковые дробилки и после дробления- на конвейеры. Выдача руды осуществляется участковыми и магистральными конвейерами к стволам шахт «Эксплуатационная» (горизонт 752м ) и «Новая» (горизонт 1070м), по которым скиповыми подъемами руда выдается на поверхность. Следует отметить, что циклично-поточная технология, внедренная на подземном руднике комбината, в настоящее время является единственной действующей в России.
Опасное наследие. Почему причины аварии на «Мире» нужно искать в прошлом
Авария на подземном руднике «Мир» отрезала от поверхности земли 151 человека. Сейчас жизни 142 из них ничего не угрожает. Ведётся спасательная операция по розыску девяти шахтёров. Почему произошло затопление шахты и можно ли было этого избежать, разбирался Лайф.
На знаменитом алмазном руднике «Мир» в Якутии продолжается спасательная операция. В пятницу утром вода из карьера прорвалась в шахту, где работал 151 человек. Почти всех шахтёров удалось поднять на безопасные отметки. Однако девять человек ещё находятся в шахте, операция по их спасению продолжается. Прокуратура и власти Якутии, Следственный комитет и Ростехнадзор теперь будут выяснять, почему в шахте с людьми появилась вода.
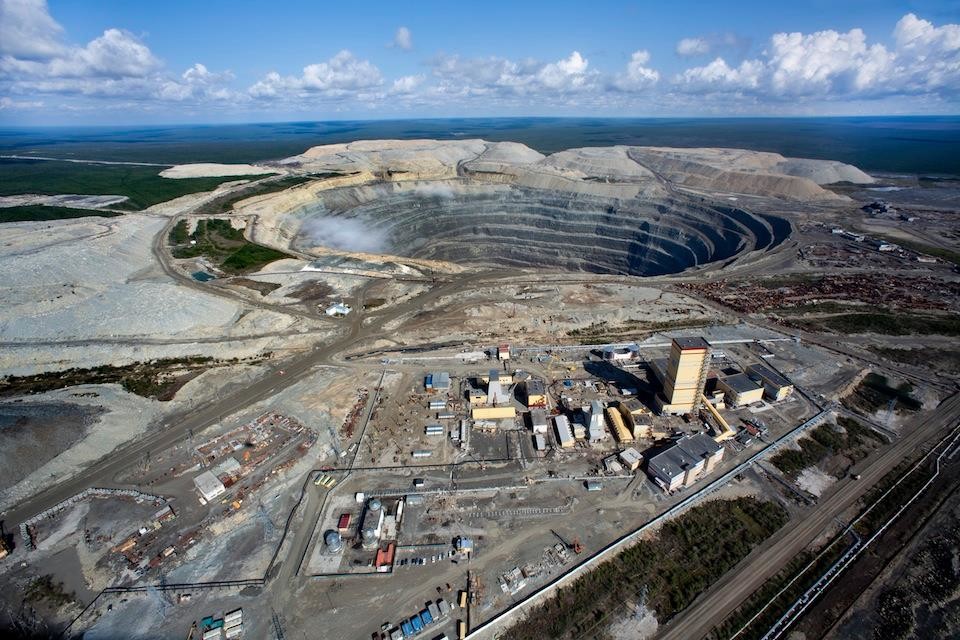
[object Object]
Крупнейшая на кимберлитовой трубке «Мир» технологическая авария произошла в 10:35 по местному времени. На горизонте минус 210 произошло подтопление насосной станции главного водоотлива № 2. На момент аварии в выработках рудника на этом уровне находился 151 человек. Ещё несколько десятков шахтёров работали выше. Первоначально, по данным паблика Mash, на связь вышли только 90 горняков, с остальными связаться не получилось. Клеть опустить в шахту также не смогли из-за сбоя электричества.
На шахте сразу же началась операция по спасению людей, которую вели сотрудники МЧС Якутии. На место аварии вылетела оперативная группа МЧС во главе с министром Владимиром Пучковым, который с президентом России сейчас находится в соседней Бурятии, а также пять отрядов горноспасателей и подземных водолазов — всего около 30 человек.
— На руднике создана группировка сил и средств МЧС России в количестве 36 человек и шести единиц техники филиала Якутский ВГСО ФГУП «ВГСЧ» и Главного управления МЧС России по Республике Саха (Якутия), спланированы мероприятия по её наращиванию, — рассказали Лайфу в МЧС.
Кроме того, глава «Алросы» Сергей Иванов вылетел в Якутию, как только стало известно, что в подтопленной шахте находятся люди.
Примерно в 13:00 была организована связь со 130 шахтёрами, находящимися в горных выработках рудника, подана электроэнергия и запущены две подъёмные установки. Ещё через полчаса вода ушла с подтопленных участков рудника. К вечеру были подняты 142 горняка. Ведутся поиски ещё девяти.
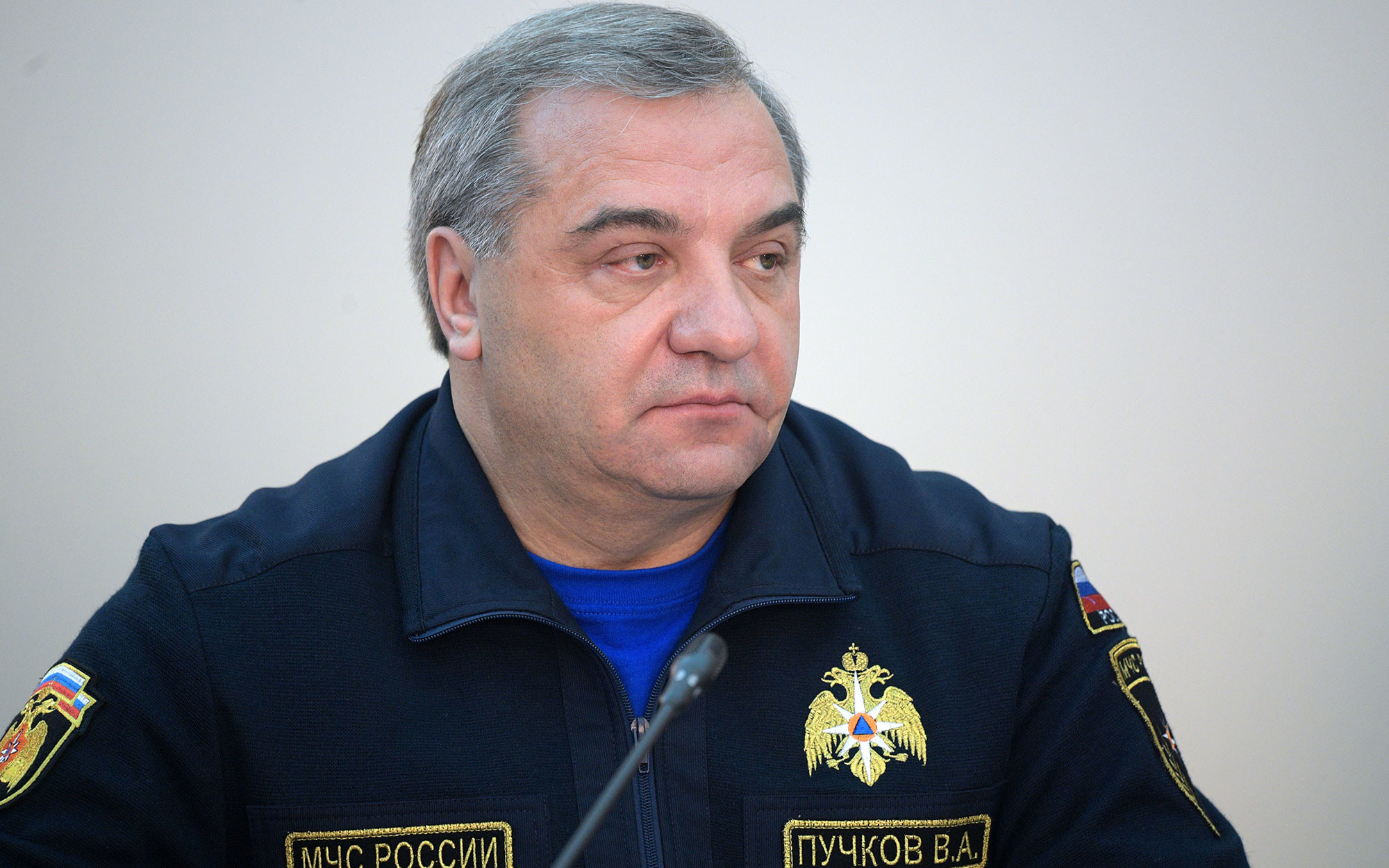
[object Object]
Разбираться с причинами аварии теперь будут Ростехнадзор, Следственный комитет, прокуратура, власти Якутии, а также специалисты самой «Алросы». В первую очередь ревизоры намерены выяснить, почему вода попала в шахту и что было сделано, чтобы этого не допустить.
— По предварительным данным, авария могла произойти из-за нарушений технологии консервации отработанных скважин, — рассказал Лайфу источник в МЧС. — Кроме того, во всех выработках должны стоять датчики, реагирующие на движение пластов, чтобы принять решение: эвакуировать людей или продолжать работу. Комиссия будет выяснять, были ли такие датчики на руднике «Мир» и как ответственные лица реагировали на их показания.
В компании «Алроса» также назвали предварительную причину сегодняшнего затопления шахты. Отмечается, что это могло быть неконтролируемое увеличение водопритока из чаши отработанного карьера в подземный рудник. В свою очередь, это случилось из-за «резкого ухудшения горно-геологических условий и размыва вмещающих пород в карьер».
Хотя предварительная версия причин аварии уже озвучена, есть и другие предположения относительно произошедшего. Корни ЧП могут скрываться в истории технологического освоения алмазного месторождения. Добыча алмазов открытым способом на «Мире» началась в 1957 году и продолжалась аж до 2001-го. За 44 года эксплуатации глубина карьера достигла 520 метров. Карьерные самосвалы, вывозившие породу, накручивали от дна до поверхности аж восемь километров пути!!! Затем встал вопрос о необходимости cтроительства подземного рудника.
В 2000 году инженеры Московского горного университета подсчитали, что разрыв между окончанием открытой и началом подземной разработки составит — в зависимости от вариантов — от двух до восьми лет. По их мнению, разработку можно было осуществлять с применением технологии с принудительным обрушением руды или с искусственным поддержанием выработанного пространства (при помощи закладки). «Алросе» надо было сделать выбор в пользу одной из технологий.
Системы с обрушением, как правило, отличаются хорошими показателями по затратам на добычу, производительности труда и интенсивности разработки месторождения. Объясняется это отсутствием процессов закладки и крепления очистного пространства. В условиях рудника «Мир» применение систем разработки с обрушением, по мнению инженеров, было практически безальтернативным, поскольку системы с закладкой не обеспечивают безопасности подземных горных работ и экономически неэффективны. Cебестоимость добычи руды на руднике «Мир» при использовании систем с закладкой составляла не менее $35/т, а при системах с обрушением — около $8/т, подсчитали в 2000 году инженеры Московского горного университета. Они даже оценили экономическую эффективность от применения систем с обрушением при разработке, которая, по их оценкам, могла составить не менее $2 млрд…. Но в то время руководство в «Алросе» выбрало более затратную и, как показала случившаяся авария, не очень безопасную cистему разработки.
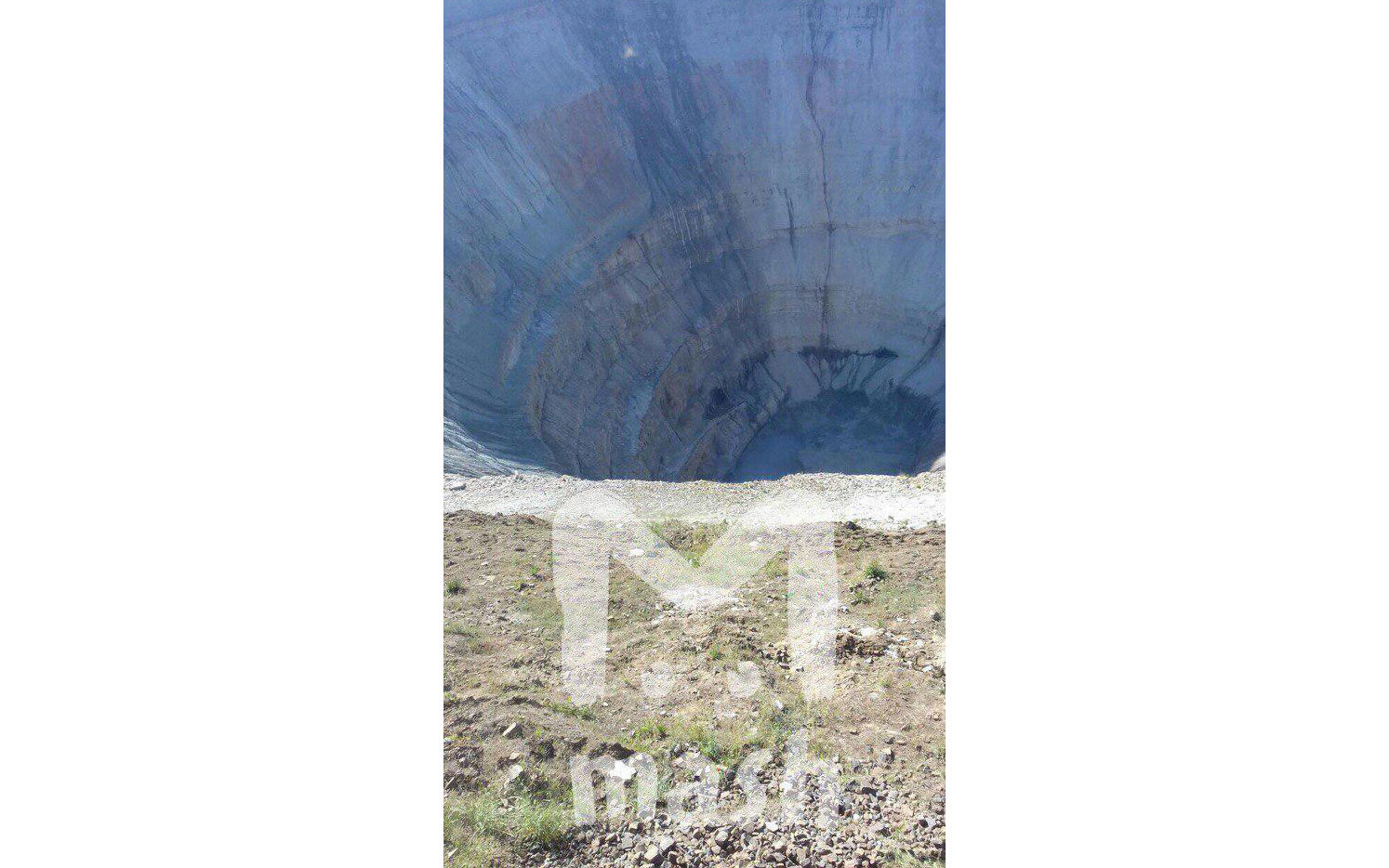
[object Object]
Эксперты разделились во мнениях относительно предопределённости происшествия из-за того, что в своё время была выбрана именно система разработки рудника с закладкой.
— У них техника тогда была как раз под такую систему. Поэтому они действовали по инерции, — предположил причину принятия решения в беседе с Лайфом источник в горной отрасли.
По его словам, для других систем разработки была нужна другая техника.
— А эта уже была куплена компанией, — добавил он.
По его словам, варианты с закладкой предполагают сохранение карьера и воды в нём. Вода должна пропускаться по каналу и выкачиваться на поверхность. Изолирующие материалы оказались не очень надёжными, поэтому вода стала поступать в подземный рудник.
— Может быть, это произошло из-за того, что это год такой. Очень много дождей было и, как результат, много подземных вод. Водопритоки поднялись.
Система откачки воды, наверное, не предусматривает таких объёмов. Что касается последующих проектов «Алросы», то «Удачный» более продуманный, предусматривает систему разработки с обрушением и с принудительным обрушением. И, конечно, там такого неожиданного эффекта не будет. Если там будет такое увеличение водопритока, то это на перехватывающих скважинах, на перехватывающих кольцах горизонта будет сказываться, но так, чтобы сюрпризом, такого не будет. Там всё фильтруется на нижних горизонтах и видно сразу, что происходит. Не так чтоб накопилось, потом ба-ба-бах — и прорвало, — cказал Лайфу источник.
Впрочем, с этой версией согласны не все.
— На тот момент, когда принималось решение о подземном способе разработки, уже была сформирована в средней части карьера водяная завеса — капитальное гидротехническое сооружение, которое удерживает давление водяного столба, создаваемого метегеро-ичерским водоносным горизонтом. Оно должно поддерживаться на весь период эксплуатации месторождения. Никакая система с обрушением не могла гарантировать устойчивость этой завесы. Просто если бы было с обрушением, то проскок воды мог быть значительно раньше. Дело не в том, что неправильный выбор системы разработки. Обеспечить устойчивость завесы могла только правильная закладка выработанного пространства при чётком соблюдении режима ведения горных работ, — прокомментировала Лайфу горный инженер, доктор технических наук, профессор, заведующий отделом теории проектирования освоения недр, главный научный сотрудник Института проблем комплексного освоения недр (ИПКОН) Марина Рыльникова.
Фото: © РИА Новости / Сергей Субботин
Кимберлитовая трубка «Мир» — карьер, расположенный в городе Мирный, Якутия.
1 / 4
Карьер глубиной 520 метров, в средней части проходит крупный подземный водоносный горизонт. Подземная река. Её перехватили по периметру путём нагнетания тампонажного бетонного раствора. И эта завеса держит порядка 100-метровой высоты напор минерализованных вод. Завесу нельзя подвергать критическим деформациям. Удерживание водяного столба — это основная задача сформированного капитального гидротехнического сооружения.
— Только системы с твердеющей закладкой могут предотвратить такие деформации, — отмечает Марина Рыльникова.
Другое дело — обеспечение режима и параметров выполнения работ по закладке выработанного пространства.
— Здесь нельзя нарушать режимы выполнения закладочных работ, своевременность заполнения пустот, должна быть особая закладка, не допускающая растворения соляных пород на контакте с алмазоносными кимберлитами. Нельзя допускать растворения соли и формирования неконтролируемых пустот, — сказала Лайфу Марина Рыльникова.
Подземный рудник «Сафьяновская медь» — Рудники ⚒ Урала
В сентябре 1985 года Исетской геологосъемочной партией ПГО «Уралгеология» в процессе планомерных геофизических работ было открыто Сафьяновское медно-колчеданное месторождение. В последующие годы месторождение было детально разведано и в 1992 году передано для промышленного освоения предприятию ОАО «Сафьяновская медь-Медин».
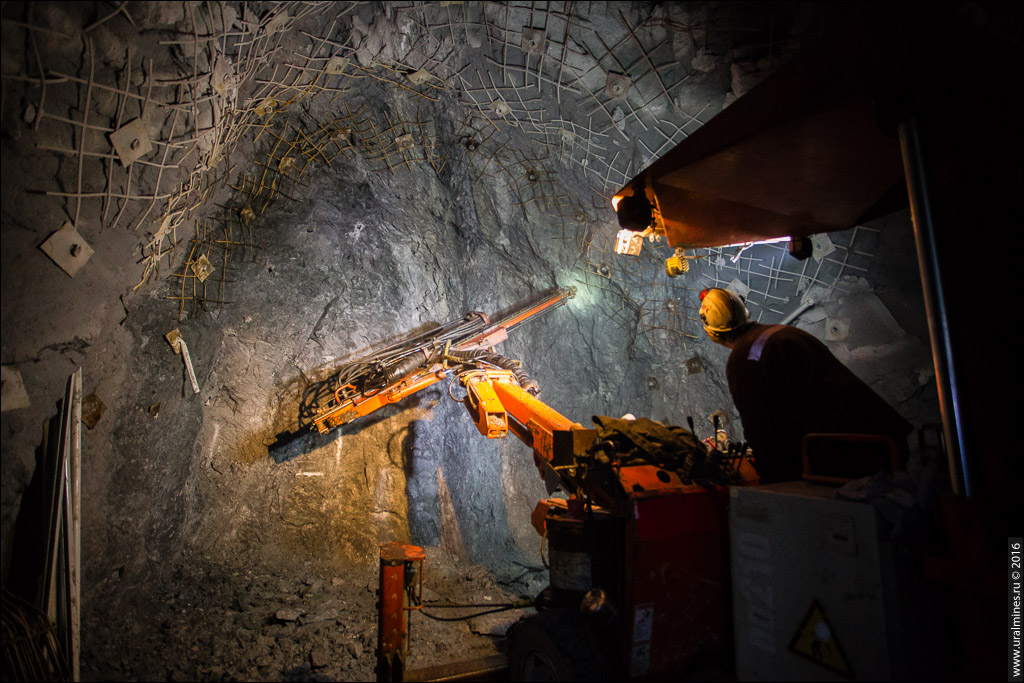
В 1994 году Сафьяновский карьер выделился в самостоятельное предприятие ОАО «Сафьяновская медь». 24 января 1994 года был торжественно погружен первый ковш породы, а первую руду добыли в конце июня этого же года.
В верхних горизонтах находилась очень качественная золото-серебряная руда с высокими содержанием полезных компонентов. К декабрю 1994 года горняки вскрыли медные руды на горизонте 197,5 м.
В 1999 году «Сафьяновская медь» вошла в состав УГМК и началось строительство первого пускового комплекса – системы водоотлива, станции нейтрализации кислых вод, склада руды, АБК и химлаборатории. Первая очередь карьера предусматривала ежегодную добычу 700000 тонн медноколчеданной руды, к 2001 году производительность карьера достигла проектной – 1 млн. тонн руды в год.
К 2003 году добыча медноколчеданной руды достигла 6,1 млн. тонн. С 2003 по 2012 год предприятие являлось филиалом ОАО «Уралэлектромедь», а с 2013 года выделилось в ОАО «Сафьяновская медь».
Сафьяновское месторождение по запасам входит в число наиболее значимых объектов на Урале.
Месторождение представляет собой сложное линзообразное тело, представленное в верхних горизонтах массивными медными и медно-цинковыми рудами, переходящих с глубиной в прожилково-вкрапленные.
Среди сплошных руд выделяются медные богатые, медные рядовые, медно-цинковые и серноколчеданные. Средние содержания металлов в руде составляют: медь – 2,52%, цинк – 0,77%, свинец – 0,09%. Кроме основных компонентов руды содержат 18 попутных компонентов – золото, серебро, селен, теллур, индий, таллий, галлий, германий, кадмий и другие.
Отработка северного фланга Сафьяновского месторождения осуществляется автомобильными съездами с внешним отвалообразованием.
Высота уступа по пустой породе составляет 12-15 метров в зависимости от крепости пород. Уступы по руде проводятся по 7,5 метров, что позволяет производить селективную выемку руды.
На транспортировке горной массы применяются автосамосвалы БелАЗ-74505, БелАЗ-485 и Komatsu.
Для отработки южного фанга месторождения в 2010 году началось строительство подземного рудника мощностью 500000 тонн в год. В 2014 году вступил в эксплуатацию первый пусковой комплекс подземного рудника – из карьера была пройдена штольня, с поверхности пройдены вентиляционный ствол до гор. -270 м и автотранспортный уклон.
Портал штольни.
Для отработки рудного тела применяется экономически эффективная подэтажно-камерная система разработки с закладкой выработанного пространства и применением самоходного оборудования. Высота этажа принята 80 м с делением на 4 подэтажа по 20 м каждый.
Проходка горизонтальных и наклонных выработок производится с помощью проходческих установок Sandvick DD210.
Телескопическая стрела позволяет производить бурение шпуров по всей площади забоя.
На стреле установлен гидравлический перфоратор мощностью 20 кВт с одновременной промывкой шпура.
Отработка месторождения предусматривается автотранспортными уклонами на 4 горизонтах: -40 м, -120 м, -200 м и -270 м.
На сегодняшний день уже пройдено около 17 км подземных выработок.
Все выработки крепятся анкерной крепью с последующим торкретированием бетоном, лишь на участках тектонических нарушений и слабых пород применяется металлическая податливая арочная крепь.
На погрузке горной массы из забоев используются дизельные доставочные машины Atlas Copco Scooptram ST1030. За одну операцию машина способна погрузить до 10 тонн горной массы.
Автомобильный орт-заезд.
Машины оснащены тремя видеокамерами в кабине и пультом дистанционного управления. Дистанционное управление позволяет оператору находится вне забоя, что обеспечивает безопасность ведения горных работ.
Погрузка руды в орте-заезде.
Транспортировка горной массы производится с помощью шахтных дизельных самосвалов МоАЗ и Atlas Copco Minetruck MT436.
Погрузка руды в автосамосвал.
Пустая порода складируется у портала штольни, перегружается в автосамосвалы и отвозится в отвалы.
Руда доставляется на перегрузочную площадку на борту карьера, где перегружается в автосамосвалы и отвозится на площадку дробильного узла.
Перегрузочная площадка на борту карьера.
БелАЗы в ожидании погрузки на дробильном узле.
После предварительного дробления руда усредняется и железнодорожным транспортом отправляется на ОАО “Святогор” и Кировградскую обогатительную фабрику.
Перевозка персонала по подземным выработкам осуществляется в специальных шахтных автобусах Майнер МТПП-24 и Paus.
После ввода в эксплуатацию скипо-клетьевого подъема на стволе, спуск-подъем рабочих и материалов будет осуществляться через шахтный ствол.
Для транспортировки руды планируется использовать автотранспортный уклон.
На данный момент отработка Сафьяновского месторождения ведется комбинированным способом. В карьере дорабатываются последние горизонты, после чего добыча руды будет производится исключительно подземным способом с одновременной рекультивацией отработанного карьера пустыми породами. На конец отработки его глубина достигнет 265 м от поверхности.
На бурении скважин в карьере работают станки 2СБШ-200 и Atlas Copco.
После бурения сетки скважин, они заряжаются ВВ.
На карьере применяется короткозамедленное взрывание.
Технологический взрыв мощностью 8 тонн взрывчатых веществ.
Отбитая руда в забое карьера.
Сафьяновский рудник является современным горнодобывающим предприятием с высокопроизводительными системами разработки и парком мощного самоходного оборудования.
Выражаю благодарность и признательность пресс-службе УГМК и руководству ОАО «Сафьяновская медь» за организацию и проведение экскурсии по предприятию.
Использованная литература:
Шереметьев Ю.С., Лещев Н.В. Сафьяновское медноколчеданное месторождение на Среднем Урале (путеводитель геологической экскурсии). 2000.
Месторождения золота Урала / В.Н. Сазонов, В.Н. Огородников, В.А. Коро-теев и др. Екатеринбург: ИГГГА, 1999.
Подземный рудник «Сафьяновская медь»:
codepeople-post-map require JavaScriptРудник «Интернациональный»: nehoroshy — LiveJournal
Кимберлитовые трубки, из которых добывают алмазы, – результат извержений подземных вулканов, произошедших миллионы лет назад. Под воздействием высоких температур и огромного давления углерод получил прочную кристаллическую решетку и превратился в драгоценный камень. Впоследствии открытие этого свойства позволило наладить производство искусственных алмазов. Но натуральные камни, разумеется, гораздо ценнее.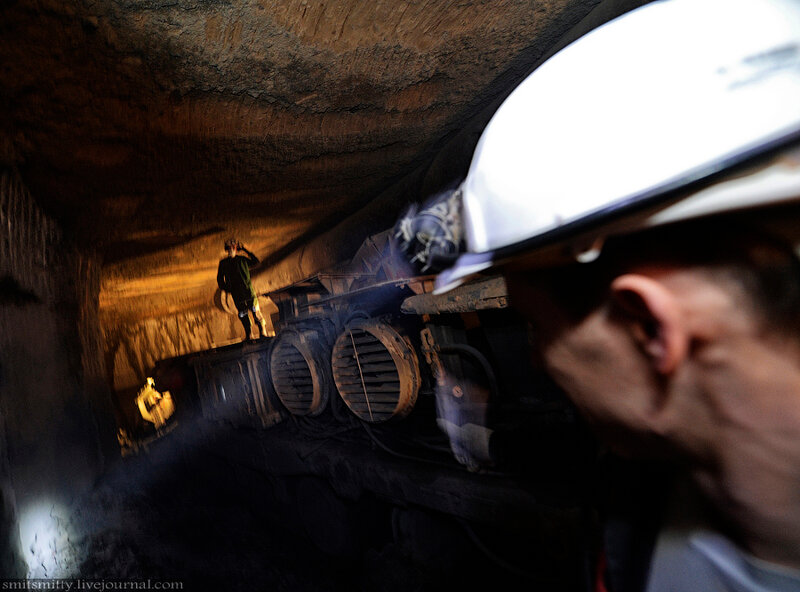
Первая масштабная промышленная добыча алмазов началась на юге Африки порядка ста лет назад. В России кимберлитовые трубки были открыты только в середине прошлого века – в Якутии. Это открытие положило начало «Алросе» – сегодня мировому лидеру по добыче алмазов. Так, прогнозные запасы компании составляют около трети от общемировых, а разведанных хватит для поддержания текущего уровня добычи в течение 25 лет без снижения качества сырья.
—
Под катом репортаж о том, как добываю алмазы на предприятии АК «АЛРОСА» ОАО в г.Мирный. Республика Саха (Якутия)
Месторождение Интернациональное было открыто в июне 1969 г., оно расположено в 15 км юго-западнее города Мирного. Кимберлитовая трубка представляет собой субвертикальное, овальное рудное тело, глубина разведанных запасов 1220 м. Добыча на руднике Интернациональный была начата открытым способом в 1971 году. Карьер в 1980 году достиг глубины 284 метра и был законсервирован до 2008 года. В середине 70-х годов началось строительство подземного рудника — алмазы трубки «Интернациональная» уникальны по своим ювелирным качествам и особенно ценятся на мировом рынке.
1.
На своих месторождениях «Алроса» добывает около 35 млн карат алмазов в год, являясь крупнейшим в мире производителем этого сырья в физическом выражении: на ее долю приходится около 97% российской добычи и 25% мировой. При этом содержание алмазов в руде кимберлитовых трубок традиционно невелико – обычно несколько карат на тонну. Якутские месторождения в этом плане выигрышны, и считаются одними из наиболее богатых по содержанию.
2.
И.о. начальника рудника «Интернациональный» главный инженер Юрий Хивинцев демонстрирует основные составляющие рудника на аксонометрической модели объекта.
3.
Кимберлитовые трубки имеют форму конуса, расширяющегося кверху, поэтому их отработку обычно начинают с карьерной добычи. Чтобы подняться со дна карьера на поверхность, самосвал по «серпантину» преодолевает путь длиной около 10 км. После достижения определенной глубины запасы в пределах карьера исчерпываются, разработка открытым способом становится нерентабельной. В среднем карьеры разрабатываются до глубины около 600 м. Однако кимберлитовые трубки залегают под землей на глубину до 1,5 км. Для дальнейшей отработки строится рудник. Подземная добыча более затратна по сравнению с карьером, однако это единственный экономически выгодный способ добраться до глубоко залегающих запасов. В перспективе «Алроса» собирается существенно увеличить долю подземной добычи алмазов.
4.
В 1999 году был введен в эксплуатацию пусковой комплекс рудника, подземный рудник был открыт 19 июля 2002 года, что стало большим достижением АЛРОСА ввиду уникальности строительства подземной шахты в данных климатических условиях. Рудник — это целый город на поверхности и хитросплетение подземных сооружений. Среди наземных объектов промышленного и бытового назначения выделяется 75-метровая башня скипового копра. Размеры рудного тела трубки «Интернациональная» в границах отработки— 90х55 м. В 2008 году вскрытие месторождения произведено двумя центрально-сдвоенными стволами. Клетевой ствол — диаметром 6,5 м, глубиной 1065 м, предназначен для спуска-подъема людей, грузов, оборудования и подачи свежей струи воздуха в рудник. Скиповой ствол — диаметром 5,5 м, глубиной 1025 м, предназначен для выдачи горной массы, подъема людей в аварийных ситуациях, подачи закладочной смеси по трубопроводам, выдачи исходящей из рудника струи воздуха. Проходка стволов осуществлена специальным методом с замораживанием грунтов буровзрывным и комбайновым способом. Система разработки трубки — камерно-целиковая с твердеющей закладкой.
5.
Заместитель главного инженера по промышленной безопасности и охране труда Евгений Колотько во время инструктажа перед спуском в рудник.
6.
Выдача шахтных самоспасателей и фонарей в ламповой
7.
Шахтный самоспасатель является средством индивидуальной защиты органов дыхания горнорабочих при подземных авариях, связанных с образованием непригодной для дыхания среды и представляет собой изолирующий дыхательный аппарат разового применения с химически связанным кислородом и маятниковой схемой дыхания. При аварийной ситуации самоспасатель способен продлить жизнь его обладателю от 60 до 180 минут в зависимости от действий. В эксплуатации этот предмет предельно прост: необходимо задержать дыхание, резким движением сорвать замок и крышку футляра, быстро поместить загубник в рот, надеть носовой зажим и выдохнуть в самоспасатель.
8.
Так же получаем фонари и каски. Фонари находятся всегда на зарядке. Одного заряда такого прибора хватает примерно на сутки.
9.
Кто-то уже собрался и готов заступать на смену.
10.
Оборудование выдается по специальным пластиковым картам с чипами.
11.
Шахтеры идут по галерее к клетевому стволу рудника.
12.
Шахтеры ожидают клеть перед спуском в рудник. Тут все строго по времени.
13.
В «лифт» втискиваемя толпой человек 20
14.
Шахтеры на одном из горизонтов подземного рудника «Интернациональный»
15.
На восьмой горизонт мы ехали семь минут. За это время шахтеры обсуждали как правильно коптить рыбу, громко спорили и шутили.
16.
8 горизонт (отметка -560м) подземного рудника «Интернациональный»
17.
Слесарь в зарядной камере рудника «Интернациональный» во время обслуживания электровоза
18.
Километр под землей! С ума сойти! Ранее я бывал на глубине 860 метров в вольфрамовом руднике Восток-2 в Приморском крае.
19.
Всяческие знаки. В темноте и достаточно узком тоннеле запросто можно встретиться с электровозом или еще какой техникой. Тут на выручку и приходит фонарь! Достаточно всего лишь несколько раз помахать головой и техника остановится.
20.
Шахтеры в камере обслуживания самоходного оборудования подземного рудника «Интернациональный». В этом помещении выполняются ремонтные работы всей техники.
21.
ПДМ на ремонте
22.
Внутри рудника очень комфортно. Воздух подается исправно, систем орошения не требуется. Не жарко и не холодно.
23.
Машинист ПДМ (погрузочно-доставочная машина) работает в забое рудника «Интернациональный»
24.
Шахтеры во время замены резца исполнительного органа проходческого комбайна
25.
В процессе разрушения горной массы резцы вращаются, благодаря чему их износ происходит практически равномерно по всех поверхности режущего конуса — они самозатачиваются. Такая конструкция резца позволяет разрушать относительно крепкие породы с меньшим по сравнению с другими конструкциями резцов расходом инструмента.
26.
27.
28.
29.
Отбойка руды в очистной ленте и погрузка в ПДМ (погрузочно-доставочная машина) в забое подземного рудника «Интернациональный»
30.
Машинист проходческого комбайна в забое рудника «Интернациональный»
31.
Машину снуют из забоя в забой
32.
Транспорт для доставки людей на рабочий горизонт выработки
33.
34.
35.
36.
37.
Маркшейдеры задают направление выработки на территории подземного рудника «Интернациональный»
38.
39.
40.
41.
42.
Шахтеры во время отдыха в нише ТБ подземного рудника «Интернациональный»
43.
44.
45.
46.
47.
48.
ВОт еще один проходческий комбайн в забое рудника «Интернациональный»
49.
Немного другой тип.
50.
Теперь нап предстоит подождать клеть и подняться наружу с порошлой сменой.
51.
Вид на карьер рудника «Интернациональный» с копра шахты
52.
Самосвалы вывозят добытую в руднике руду на обогатительную фабрику
53.
Про фабрику будет отдельно.
54.
На копре установленна звезда, которая загорается в момент когда будет выполнен план.
55.
Вид на кимберлитовую трубку алмазного карьера «Интернациональный» с высоты копра.
56.
Основные предприятия компании расположены в Западной Якутии, на территории четырех районов Республики Саха (Якутия) – Мирнинского, Ленского, Анабарского, Нюрбинского – в одном из наиболее суровых регионов планеты, с резко континентальным климатом, большим перепадом температур, в зоне вечной мерзлоты. В некоторых районах зима длится до 8 месяцев, температура зимой порой опускается до -60 С. Поэтому большая часть техники сделана под заказ – это машины, адаптированные к работе в условиях низких температур. В итоге работы на месторождениях ведутся круглый год в любых погодных условиях.
Тематические репортажи у меня в блоге:
Кузбасс. Шахта «Южная»
Шахта «Южная» расположена на Глушинском каменноугольном месторождении, общие запасы которого составляют около 450 млн. тонн угля. Промышленные запасы предприятия составляют 100 млн. тонн. При проектной мощности 2 млн. 400 тыс. тонн угля в год их хватит почти на 50 лет бесперебойной работы.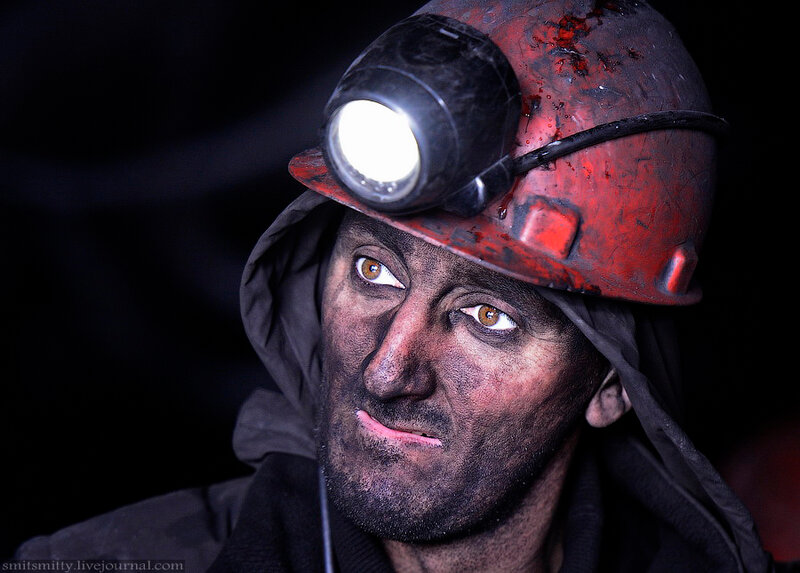
Шахта была построена за три с половиной года и уже в этом году успела отметить пятилетний юбилей со дня открытия. Сегодня «Южная» является примером современного, безопасного угледобывающего предприятия, оснащенного по последнему слову техники. С момента запуска предприятия шахтеры выдали- 11,6 млн тонн угля и прошли – 44 км горных выработок.
Вольфрамовый рудник Восток-2
Значится так, нам KFSS.ру повезло побывать на самом большом Вольфрамовом руднике в стране, который находится за 700 км от столицы Приморья.Маршрут Владивосток-Восток-2 является самым длинным в крае…это около 13 часов сидения на жопе в неудобном автобусе, в жаре..но это стоило того!
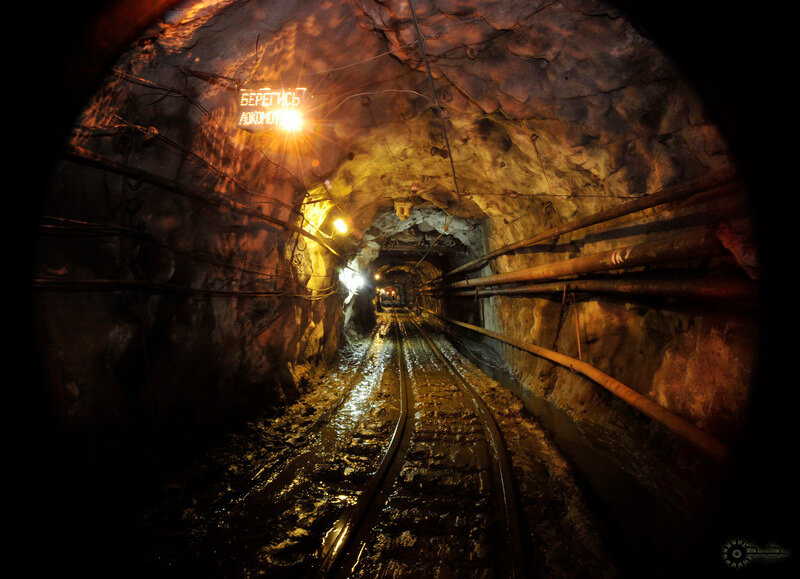
—
Честичное текстовое сопровождение с сайта: swalker.org
—
Спасибо за внимание!
—
-Использование фотоматериала разрешается только при моем личном согласии.
-Если вы используете фотографии в некоммерческих целях не забывайте ставить активную ссылку на мой журнал.
-Все снимки, размещенные в этом журнале, моего авторства, если не написано обратное.
-Текстовое описание объектов использовано из открытых источников
smitsmitty
прииски, шахты, штольни и карьеры
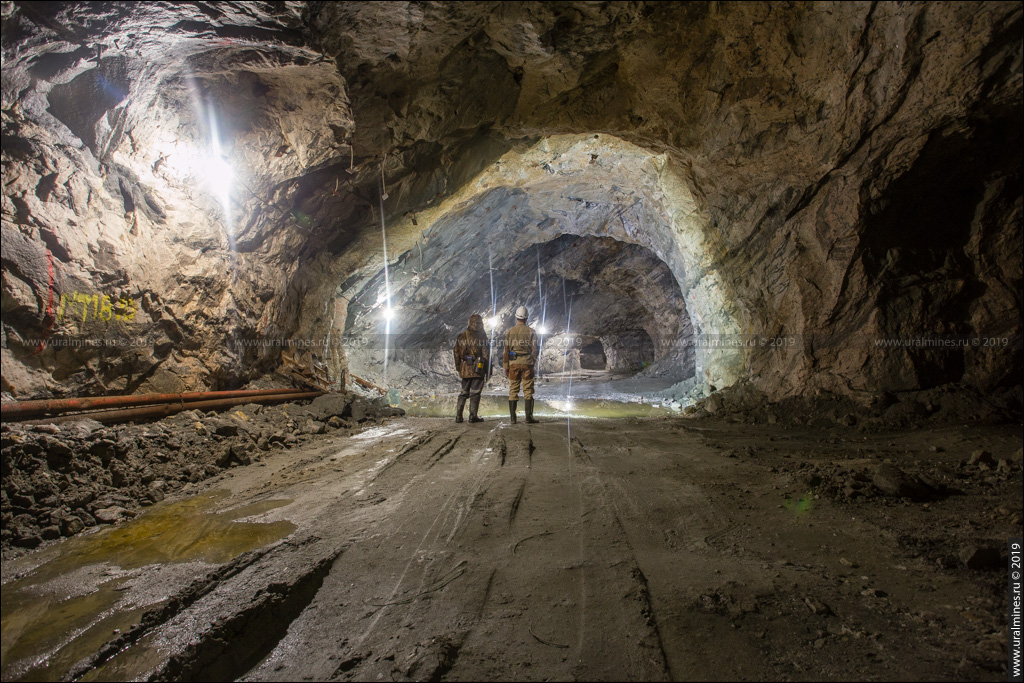
Кыштымское месторождение гранулированного кварца расположено на восточном склоне южной части Среднего Урала, в 15 км к западу от г. Кыштым. Кварцевые жилы в Кыштымском горном округе были известны еще с XVIII века. Прозрачные, полупрозрачные и окрашенные разности стекловидного кварца добывались старателями как ограночный материал, неотличимый в изделиях от горного хрусталя и раухтопаза. Гранулированный кварц использовался […]
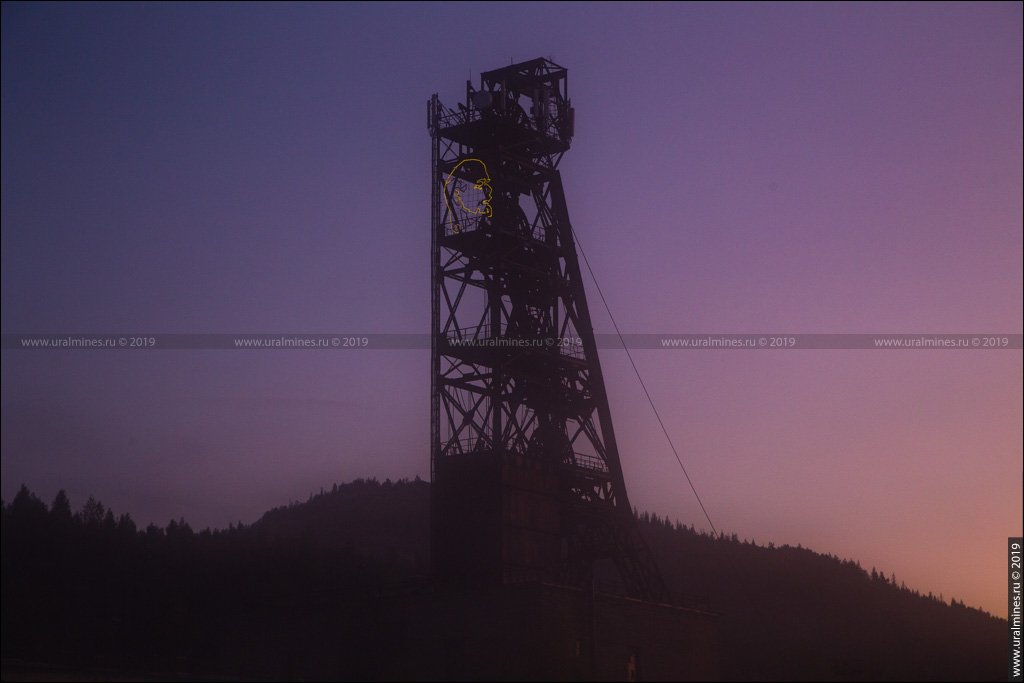
Бакальское рудоуправление – одно из старейших горных предприятий Урала. Летом 1756 года рудознатцем Петром Рябовым с помощью местных башкир было обнаружено 10 выходов бурого железняка на склонах горы Буландиха в долине реки Бакал.
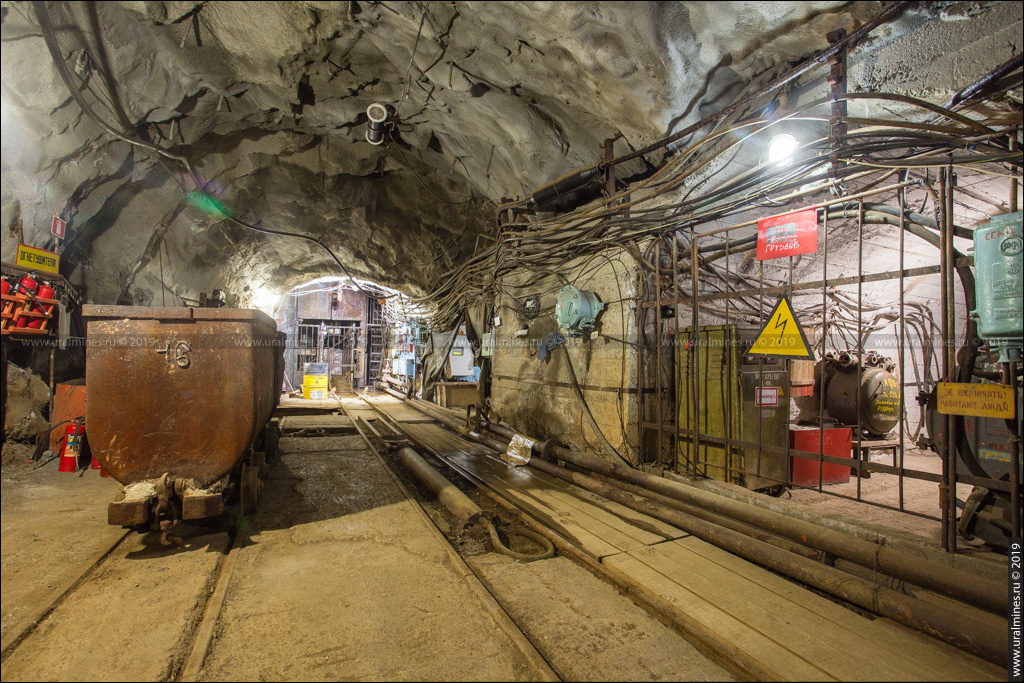
Баженовское месторождение хризотил-асбеста является крупнейшим в мире и было открыто в 1885 году. Систематическая разработка Баженовского месторождения началась в 1889 году, когда было добыто 30 тонн асбеста.

Саткинское месторождение магнезита расположено в Челябинской области в г. Сатка и является одним из крупных эксплуатируемых месторождений магнезита в России.
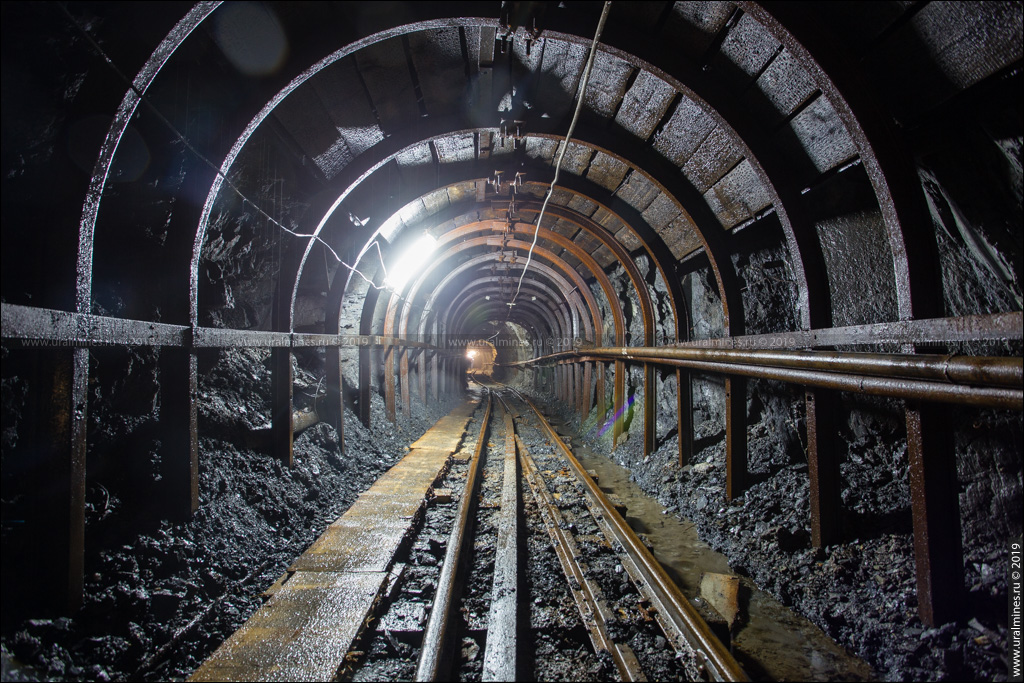
Сарановское месторождение хромитовых руд расположено на западном склоне Среднего Урала в Горнозаводском районе Пермского края, в 6 км к северу от ст. Лаки Свердловской железной дороги и располагается в пределах меридионально вытянутой возвышенности при населенном пункте п. Сараны.
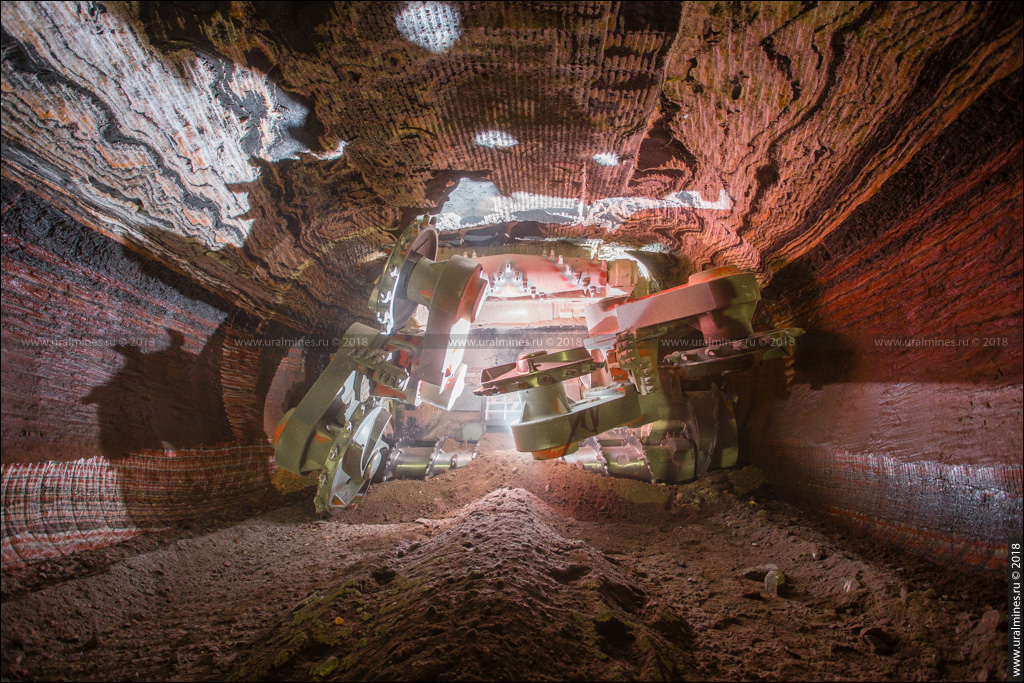
Верхнекамское месторождение калийно-магниевых солей (ВКМКС) расположено на левом берегу р. Камы. В административном отношении оно находится на территории Чердынского, Красновишерского, Соликамского, Усольского и Добрянского районов, а также на территориях, подчиненных городам Березники и Александровску. По запасам это самое большое калийное месторождение России, занимающее второе место среди крупнейших в мире (уступает по разведанным запасам только аналогичному […]
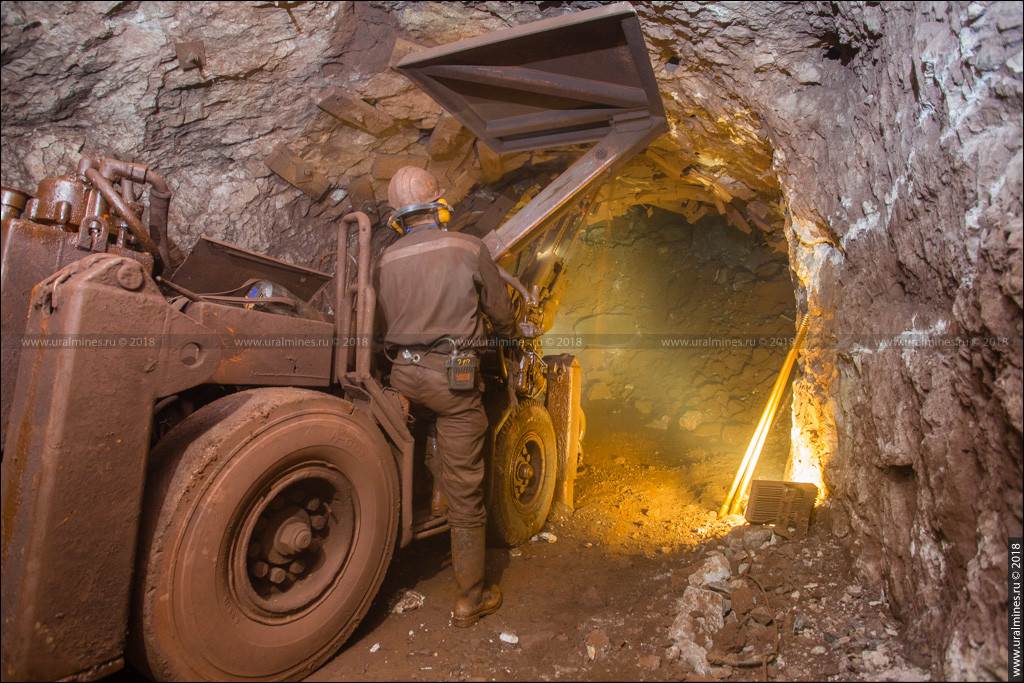
Бокситы на Северном Урале были открыты в 1931 году геологом Н.А. Каржавиным. О своем открытии Н.А. Каржавин в газете «Пролетарий» за 1934 год писал: «Я немедленно отправился в Федоровский музей: бокситы района Петропавловского завода оказались весьма опрятно уложены не только в шкафах музея, но и в неразложенных коллекциях недавних сборов. Их анализ, проведенный в Уральском […]
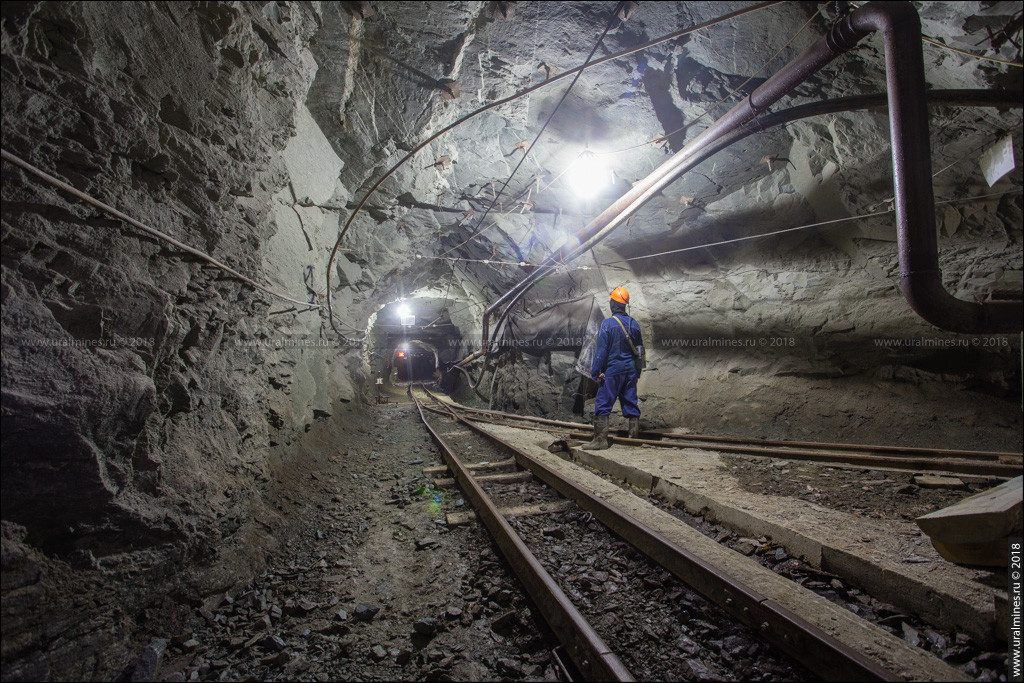
С момента нашего посещения шахты «Северная» Березовского рудника в марте 2017 года горняки выполнили значительный объем восстановительных и горно-подготовительных работ на горизонте -612 м.
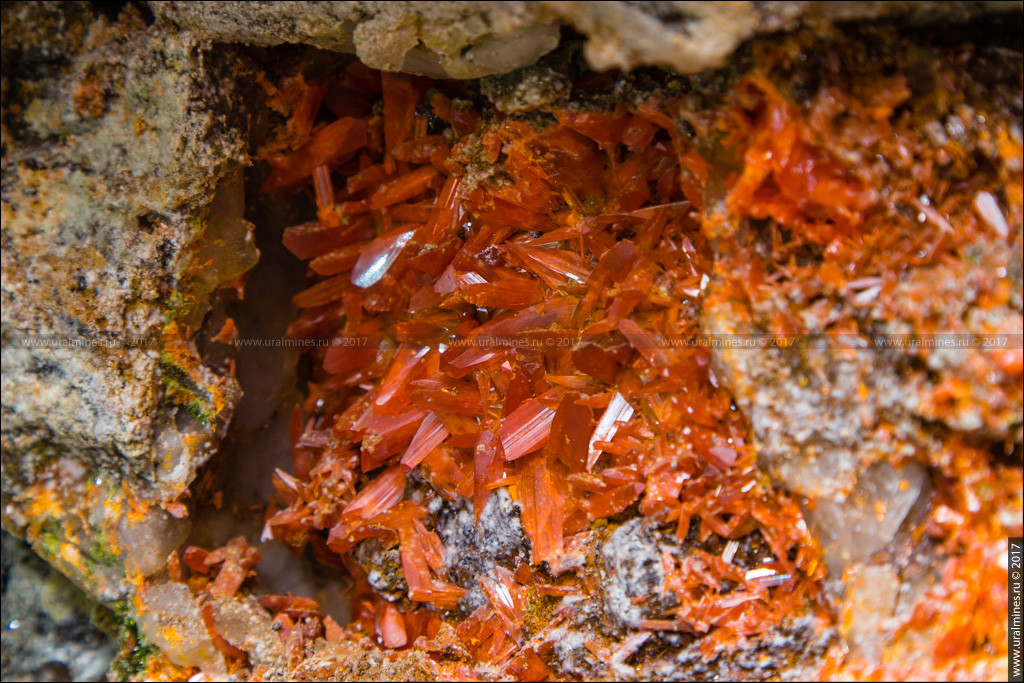
С первых лет разработки Березовские золотые рудники вызвали интерес отечественных и иностранных ученых. Среди них можно указать посетивших месторождение крупнейших натуралистов прошлого: П.С. Палласа, А. Гумбольдта, Г. Розе и русских академиков – И. Севергина, Н. Кокшарова, П. Еремеева, А. Карпинского. На Березовском месторождении впервые описаны и получили название широко распространенные горные породы – березит и […]
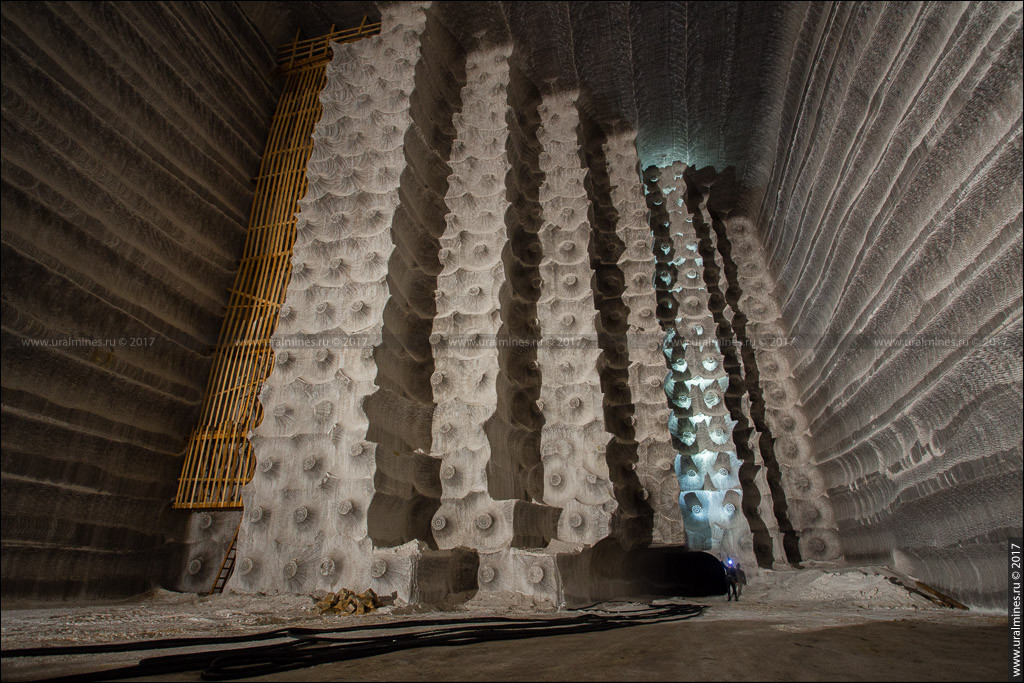
Илецкое месторождение каменной соли, славящееся как по чистоте самого продукта, так и по мощности залегания было известно со времен глубокой древности. Время открытия Илецкого месторождения и начало разработок соли точно неизвестно. Согласно преданию, открытие соли приписывается прикаспийским народам – ногайцам, кочевавшим еще в XVI веке на пространных бухарских степях.
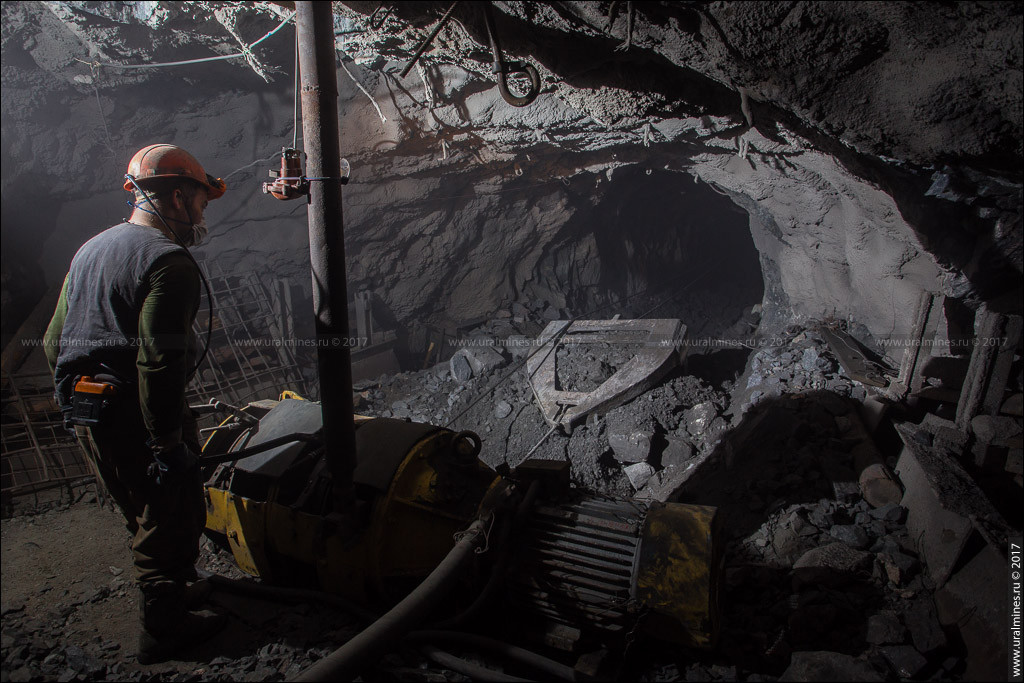
Гора Благодать принадлежит к числу старейших из разрабатываемых на Урале железорудных месторождений, руды которого уже давно заслуженно славились своими высокими качествами. Гороблагодатское месторождение железных руд было открыто в 1728 году Степаном Чумпиным и начало разрабатываться с 1735 года открытым способом.
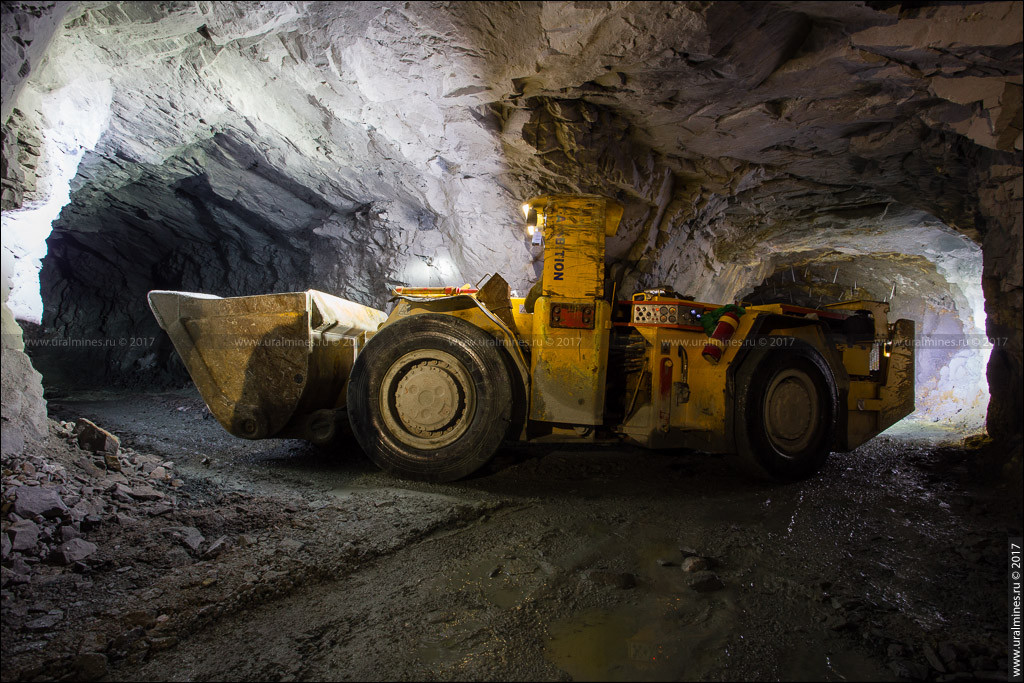
Шахта «Северная» является самой современной шахтой Берёзовского рудника и разрабатывает северную часть одноименного золоторудного месторождения.
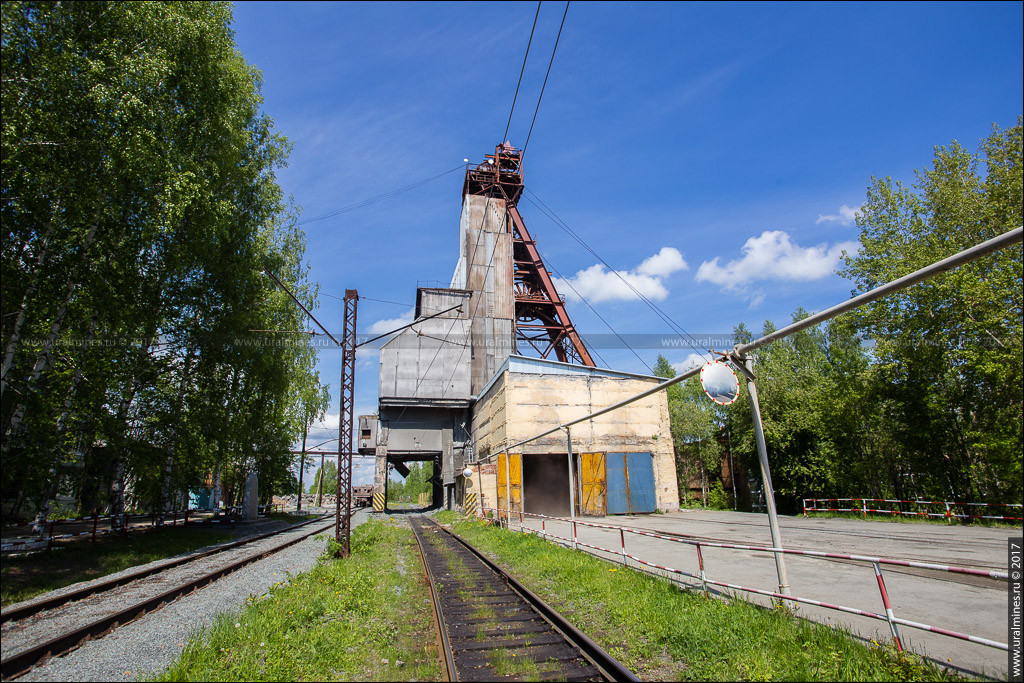
Естюнинское месторождение входит в Тагильскую группу железорудных месторождений и расположено в 8 км северо-западнее г. Нижнего Тагила. Месторождение было открыто в 1900 году на горе Естюниной и первоначально периодически отрабатывалось в 1901-1902 годах несколькими карьерами на северном склоне горы. Добыча велась в небольшом объеме и данных о ней не сохранилось. При этом на глубину разведок […]
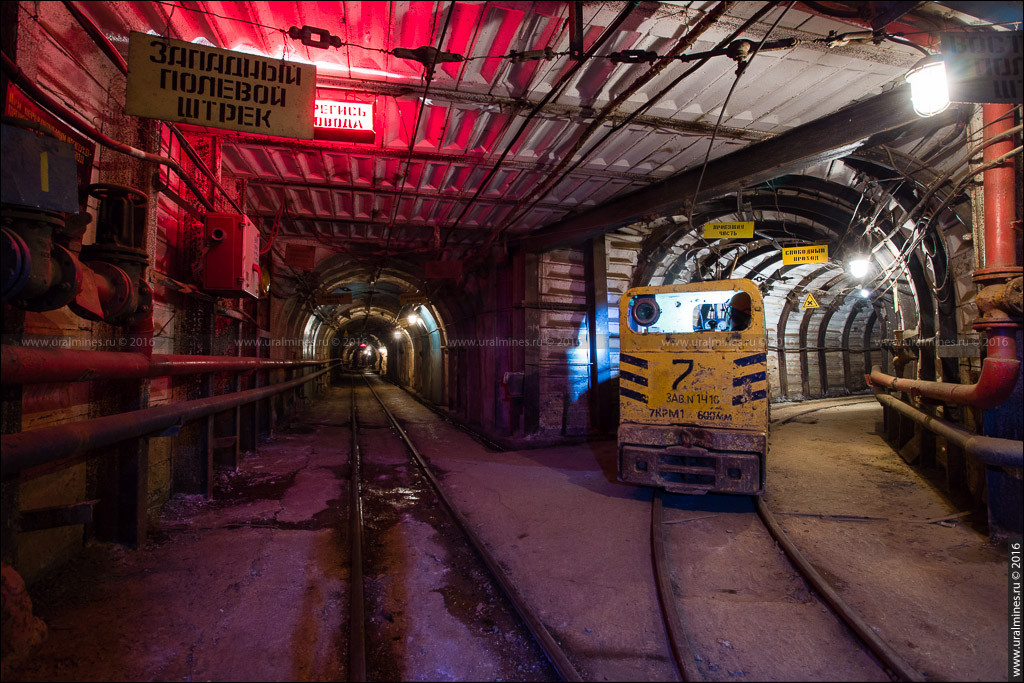
Впервые в России изумруды были найдены в декабре 1830 года крестьянином Белоярской волости Максимом Степановичем Кожевниковым на реке Токовой. Эта уникальная находка послужила толчком к поискам изумрудов в окрестностях Сретенского прииска.
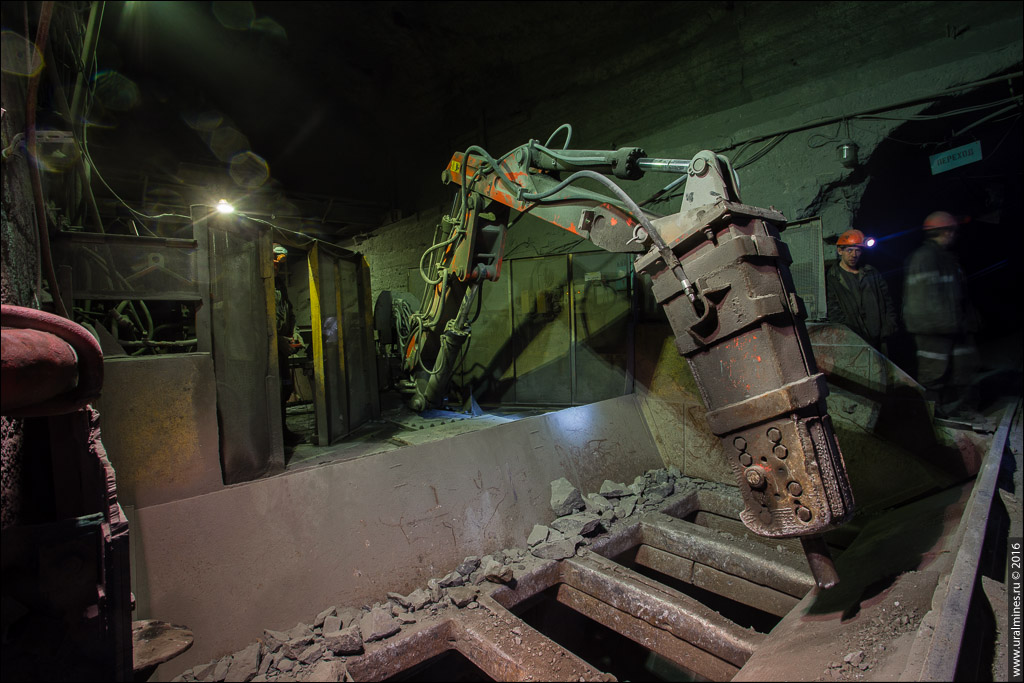
Высокогорское железорудное месторождение было известно местными жителями-вогулами еще в XVII веке. Официальная заявка о наличии железных руд на горе Магнит (Высокой) была подана Яковом Савиным в 1696 году. В мае 1697 года Виниус писал с Урала за границу Петру I: «Я сыскал зело добрую руду из магнита железную, какой лучше быть невозможно, и во всей […]
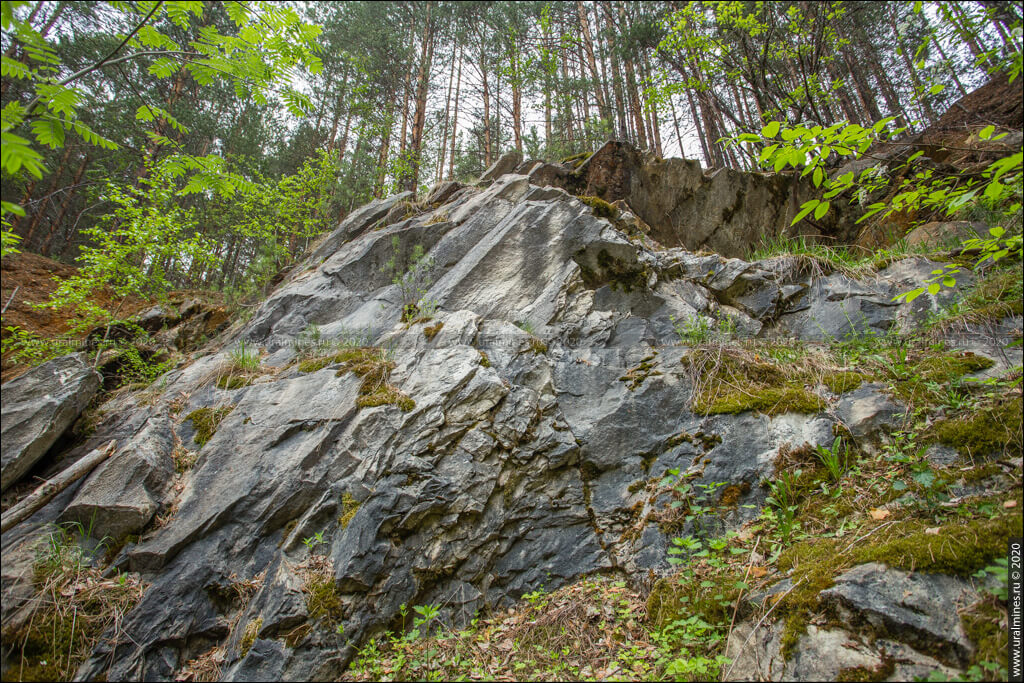
Фоминское месторождение желтого и золотистого мрамора расположено в Сысертском районе Свердловской области, около д. Фоминой, в бывшей Каменской даче.
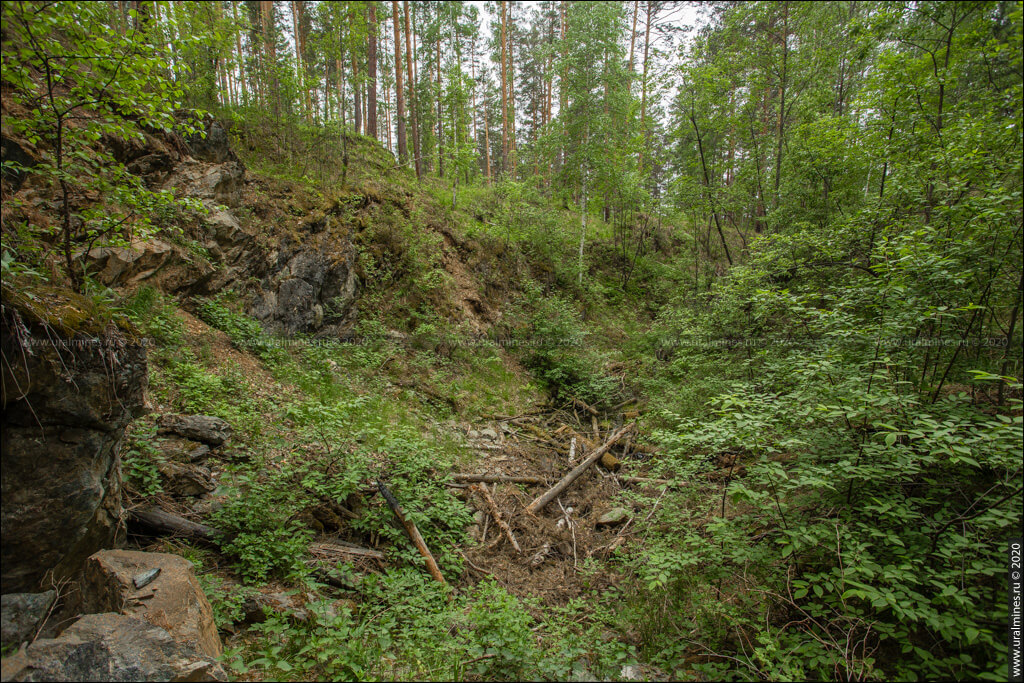
Чусовской хромовый рудник находится в 57(99) квартале бывшей Северской дачи.
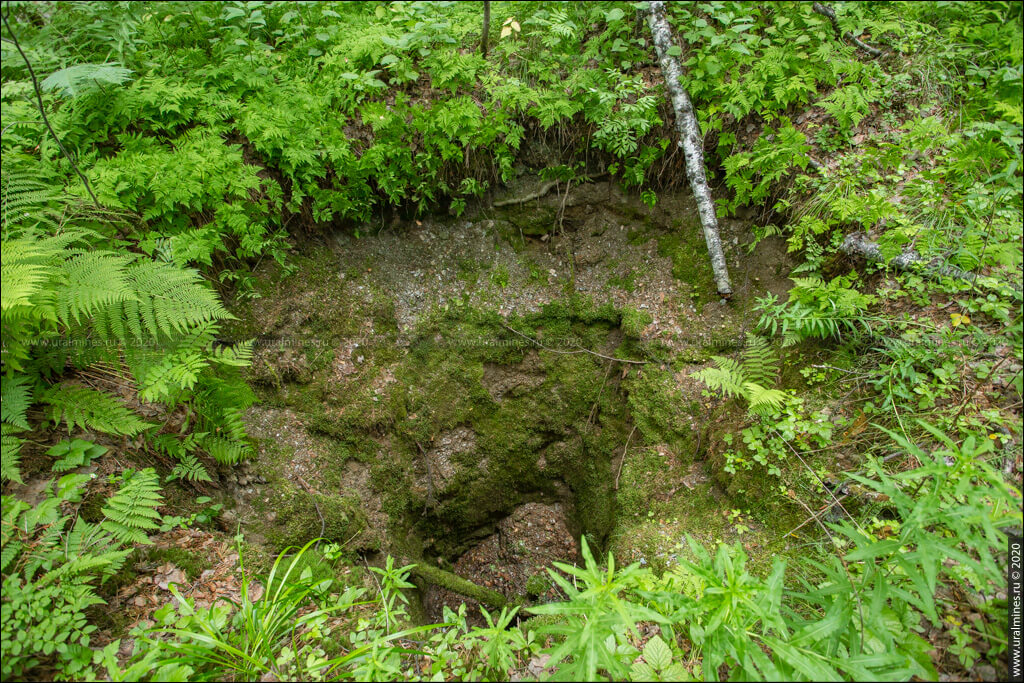
Белоглазовское месторождение расположено в окрестностях Горного Щита и представлено кварцевой жилой, залегающей в полосе метаморфических сланцев.
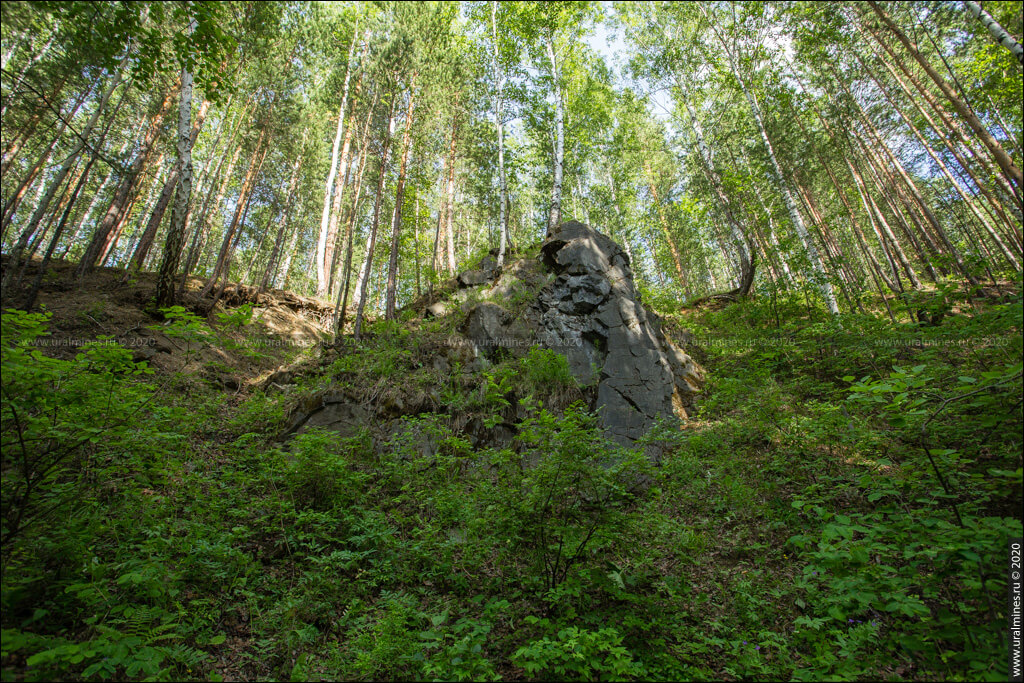
Палкинское (Оброшинское) месторождение известняка расположено в черте г. Екатеринбурга, на берегу Верх-Исетского пруда и приурочено к пластообразной залежи мраморизованных известняков (мраморов) кунгурковской свиты.
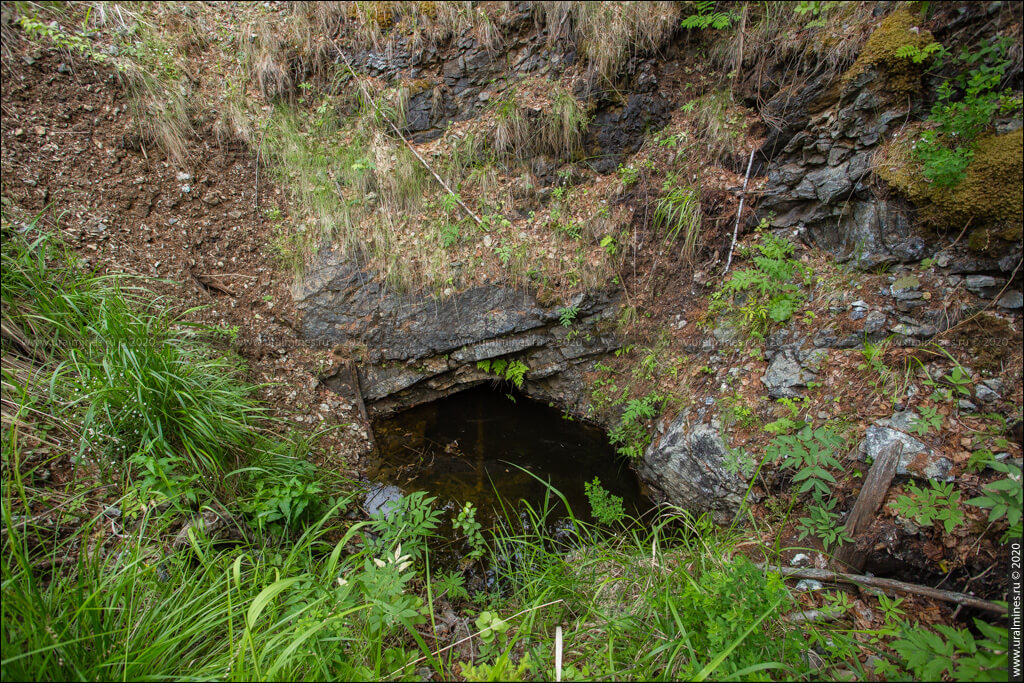
Шеромский хромовый рудник расположен в Шеромских горах бывшей Билимбаевской дачи.
Мир (кимберлитовая трубка) — Википедия
Кимберлитовая трубка «Мир» — коренное месторождение алмазов, открытое в 1955 году. Данное месторождение алмазов стало вторым коренным месторождением алмазов в Якутии после открытия в 1954 году первой в Советском Союзе кимберлитовой трубки «Зарница» геологами Н. Н. Сарсадских и Л. А. Попугаевой[1], но первой начала разрабатываться трубка «Мир». Месторождение разрабатывалось вначале открытым способом, а затем по мере углубления карьера постепенно разработка перешла на подземный способ добычи алмазов. Карьер имеет глубину 535 м и диаметр 1,2 км. Добыча алмазоносной кимберлитовой руды открытым способом прекращена в июне 2001 года. С 2009 года по август 2017 года добыча руды велась только на подземном руднике «Мир»[2], но он в данный момент затоплен из-за аварии — в результате добыча алмазов остановлена на неопределённый срок[3].
У этого термина существуют и другие значения, см. Мир.История открытияПравить
Кимберлитовая трубка была открыта 13 июня 1955 года по прогнозной карте, составленной геологом Н. В. Кинд, геологами Амакинской экспедиции Ю. И. Хабардиным, Е. Н. Елагиной и В. П. Авдеенко. Знаменитая радиограмма, переданная ими руководству экспедиции об обнаружении кимберлита, была кодированной, с отсылкой к культурному термину «трубка мира»[4]:
Закурили трубку мира, табак отличный. Авдеенко, Елагина, Хабардин.
— Радиограмма об открытии алмазной трубки «Мир». 13 июня 1955 г.
За открытие трубки «Мир» Ю. И. Хабардин удостоен Ленинской премии, Е. Н. Елагина была награждена почётной грамотой и дипломом «Первооткрыватель месторождения», а также стала почётным гражданином Мирного[5].
Геологическое строениеПравить
Трубка «Мир» находится в Мало-Ботуобинском алмазоносном районе. Кимберлитовая трубка «Мир» представляет собой крутопадающее трубообразное тело, до глубины 300 м (отметка +30 м) — конусообразное. Площадь поперечного сечения рудного тела уменьшается с глубиной и на глубине 900 м переходит в даечное тело. Трубка сложена кимберлитовыми породами, образовавшимися в результате трёхфазного внедрения кимберлитовой магмы. Породы разных фаз мало отличаются по составу, физико-механическим свойствам и алмазоносности.
Газоносность, битуминозность и нефтеносность сильно пористых слоёв, вмещающих карбонатные породы и, в меньшей степени, кимберлиты, обусловила отнесение подземного рудника к опасным по газонефтепроявлениям. В связи с этим, проходка подземных выработок в мощных карбонатных пластах осуществляется после обуривания массива пород перед забоем выработок опережающими дегазационными скважинами.[6]
Разработка в карьереПравить
Карьер «Мир» до 2001 годаВ 1957 году началась добыча алмазов открытым способом, продолжавшаяся 44 года (до июня 2001 года[7]). Рядом с карьером образовался посёлок Мирный, ставший центром советской алмазодобывающей промышленности. Крупнейший алмаз, найденный в России, был добыт в карьере «Мир» 23 декабря 1980 года. Он весит 342,5 карата (более 68 г) и называется «XXVI съезд КПСС»[8]. В последние годы карьерные грузовики «накручивали» по спиралевидной дороге 8 км от дна до поверхности.
В ходе своей работы карьер 3 раза реконструировался, были созданы уникальная тампонажная завеса, предотвращавшая поступление агрессивных рассолов из Метегеро-Ичерского водоносного комплекса, а также система водоотлива 32250 м³ воды в сутки (около 1 млн м³ в месяц).
За годы разработки открытым (карьерным) способом из месторождения добыто алмазов, по неофициальным данным, на 17 млрд долларов США, вывезено около 350 млн м³ породы.
Разработка в рудникеПравить
Геологическая разведка показала, что глубина залегания алмазов превышает километр, поэтому в настоящее время компания АЛРОСА, разрабатывающая месторождение, строит на месторождении подземный рудник. Для строительства подземного рудника и будущей безопасной отработки верхних подземных горизонтов дно законсервированного карьера было засыпано специальным предохранительным слоем породы. Эта «подушка», или «целик», не поддаётся разрывным давлениям, её толщина — 45 метров.
Из кимберлитовой трубки горняки планируют добывать подземным способом алмазосодержащую руду в течение 34 лет. Рудник, первая очередь которого введена в строй в 2009 году (7 марта 2002 года была начата проходка клетевого ствола рудника, в августе 2003 года — скипового), имеет проектную мощность один миллион тонн руды в год.[9]
Мирнинский горно-обогатительный комбинат является старейшим предприятием компании АЛРОСА. Он находится в городе Мирный и был основан в 1957 году в связи с началом освоения месторождения кимберлитовой трубки «Мир». В настоящее время ГОК разрабатывает подземным способом коренные месторождения трубок «Мир» и «Интернациональная», а также ряд россыпных месторождений. Руда, поступающая со всех добывающих предприятий ГОКа, проходит обогащение на фабрике № 3[10], проектная мощность которой составляет 2 миллиона тонн руды в год.
Структура и характеристики производственных объектовПравить
Смотровая площадка. За основу взята ходовая часть карьерного экскаватора ЭКГ-4УПодземный рудник «Интернациональный»Править
Рудник начал работу в 1999 году и в 2002 году вышел на полную проектную мощность в 600 тысяч тонн руды в год[11]. В 2014 году рудник добыл 3,862 миллиона карат алмазов. Открытая добыча на месторождении была завершена в 2011 году.
Алмазы «Интернационального» уникальны по своим ювелирным качествам и особенно ценятся на мировом рынке. Рудник имеет самое высокое содержания алмазов в руде. С содержанием на уровне 8,09 карат на тонну его запасов достаточно для ведения добычи в течение следующих 27 лет[12].
Добыча на руднике «Интернациональный» ведётся с использованием механизированной слоевой системы разработки с закладкой. Отбойка руды выполняется комбайнами. Погрузочно-доставочные машины доставляют руду до рудоспусков, затем она транспортируется в вагонетках по откаточному горизонту до капитального рудоспуска, через который руда поступает в основной ствол и затем выдаётся на поверхность.
Подземный рудник «Мир»Править
Рудник «Мир» стал не менее уникальным, чем работавший на месторождении до 2001 года карьер. Ввод в эксплуатацию подземного рудника начат в 2009 году[13]. Мощность рудника «Мир» составляет 1 миллион тонн руды в год. В 2014 году рудник добыл 1,463 миллиона карат алмазов. Горные работы ведутся с использованием механизированной слоевой системы разработки с закладкой выработанного пространства. Отбойку руды осуществляют комбайны, погрузочно-доставочные машины выполняют погрузку и доставку руды от добычных участков до одного из двух рудоспусков, обеспечивающих перепуск руды на другой транспортный горизонт[14].
Дражный флотПравить
Особенностью комбината является единственный в РФ и в компании АЛРОСА дражный алмазный флот, представленный тремя драгами[15]. Эти плавучие комплексы перемещаются по руслу реки Ирелях, поднимая с речного дна тонны алмазоносных песков, проводя их первичное обогащение.
Данные в этой статье приведены по состоянию на 2013-2014 годы. Вы можете помочь, обновив информацию в статье. |
В зоне расположения трубки Мир проходит Метегеро-Ичерский водоносный горизонт[16], который был вскрыт ещё при отработке руды карьером. По проекту подземной отработки месторождения вся вода из карьера должна непрерывно выкачиваться и закачиваться в разломы, которые найдены геологами в земной коре. Скапливающаяся в карьере вода также подтапливает расположенный под землёй рудник.
В целях безопасности вода непрерывно выкачивается насосами из карьера. Сейчас[когда?] ведутся дополнительные работы, в результате которых весь приток воды должен стать управляемым. В частности, будут запущены сооружения для перехвата воды на верхних горизонтах. Таким образом, рудник полностью будет соответствовать всем требованиям безопасности.
Интересные фактыПравить
- 23 декабря 1980 года в карьере «Мир» был добыт крупный ювелирный алмаз весом 342,5 карата, названный в 1981 году в честь предстоявшего XXVI съезда КПСС[17].
- В марте 2002 года в карьере трубки «Интернациональная» добыт алмаз «Президент» весом 79,9 карат[18].
- Вопреки всеобщему представлению, карьер трубки «Мир» не является крупнейшим. Он имеет глубину 535 метров и диаметр 1,2 км, по этим параметрам он значительно уступает карьеру трубки «Удачная», который по поверхности имеет размер 1600 х 2000 метров, а в глубину — 640 метров.
9 октября 2012 года на руднике «Мир» произошёл обвал. Обвалился закладочный материал площадью 20 метров. На момент аварии на руднике находилось 110 человек. В результате обвала погиб 1 человек. 109 работников шахты самостоятельно вышли на поверхность.[19]
15 апреля 2013 года на руднике «Мир» произошёл обвал породы и один человек погиб.[20]
4 августа 2017 года на шахте произошел прорыв воды. В шахте находились 151 человек. Оперативно были эвакуированы 142 горняка, еще одного спасли на следующий день. Поиски оставшихся в выработке восьми человек безрезультатно продолжались около трёх недель, затем были прекращены[21][22][23][24].
Рудник законсервирован — если добыча и возобновится, то не раньше чем через несколько лет[23][24].
- ↑ 50 лет со дня открытия первой в Советском Союзе кимберлитовой трубки “Зарница” геологом Л.А. Попугаевой (рус.) (недоступная ссылка — история ). Национальная библиотека Республики Саха. Дата обращения 13 июня 2013.
- ↑ Мирнинский ГОК (рус.). Сообщество горных специалистов. Дата обращения 13 июня 2013.
- ↑ NEDRADV || Новости || 13.11.2017 // Причиной трагедии на «Мире» стали нарушения в проекте — nedradv.ru
- ↑ Ежедневная республиканская газета «Якутия» — Екатерина Елагина, закурившая трубку «Мир» (недоступная ссылка)
- ↑ Первооткрывателю трубки «Мир» Екатерине Елагиной исполняется 80 лет
- ↑ Отчёт независимых экспертов о запасах и ресурсах месторождений алмазов Группы компаний «АЛРОСА», с. 15
- ↑ Дальневосточный геологический институт — Трубка Мир, хронология (неопр.) (недоступная ссылка). Дата обращения 3 сентября 2008. Архивировано 5 декабря 2008 года.
- ↑ Евгений Щигленко, Трубка «Мира» Архивная копия от 28 мая 2012 на Wayback Machine ГЕО, сентябрь 2007
- ↑ Алроса / Мирнинский ГОК
- ↑ Якутск | Третья фабрика Мирнинского ГОК вышла из планового ремонта — БезФормата. Ru — Новости
- ↑ Якутия. «АЛРОСА» вывела на проектную мощность первый в России подземный алмазный рудник «Интернациональный». — Экономика / Финансы Новости — ИА REGNUM
- ↑ Рудник Интернациональный (Мирнинский ГОК, Алроса)
- ↑ Введён в строй подземный алмазный рудник «Мир»
- ↑ Как «Алроса» добывает алмазы (фото) — Фото № 10 (неопр.) (недоступная ссылка). Дата обращения 6 августа 2014. Архивировано 8 августа 2014 года.
- ↑ Прииск «Ирелях»: ледоуборка перед промсезоном-2013 (неопр.) (недоступная ссылка). Дата обращения 6 августа 2014. Архивировано 8 августа 2014 года.
- ↑ Применение электрохимической защиты с целью увеличения сроков эксплуатации подземного горного оборудования на рудниках АК «АЛРОСА»
- ↑ XXVI съезд. Знаменитый алмаз
- ↑ Якутия. На одной из фабрик АК «АЛРОСА» добыт алмаз «Президент» — Политика, выборы, власть — Новости — ИА REGNUM
- ↑ News.Ykt.Ru: Обвал на руднике «Мир», есть пострадавший
- ↑ РИГ SAKHAPRESS.RU / На руднике «Мир» в Якутии произошёл обвал породы: погиб человек — Пресс-служба ГУ МЧС России по РС (Я)
- ↑ Первые итоги расследования аварии на руднике «Мир» в Якутии представят в течение месяца
- ↑ Альпинисты не установили связь с горняками на руднике «Мир» в Якутии (рус.). runews24.ru. Дата обращения 9 августа 2017.
- ↑ 1 2 У аварии на руднике «Мир» есть фамилия, имя и должность — YKTIMES.RU
- ↑ 1 2 Что будет делать «Алроса» после потери рудника «Мир» в Якутии
- Хабардин Ю. И. Воспоминания первооткрывателя: Путь к алмазной трубке. — М.: Геоинформмарк, 1999. — 275 с.
Удачнинский ГОК | АЛРОСА
Распечатать PrintРазработка трубки «Удачная» началась в 1967 году в составе горно-обогатительного комбината «Айхалалмаз». В 1979 году основан Удачнинский горно-обогатительный комбинат (ГОК). Это градообразующее предприятие города Удачный, который расположен в 15 км от Полярного круга. Численность УГОК превышает 3900 человек. В состав комбината входят горные, обогатительные, транспортные, ремонтные и вспомогательные подразделения.
В 2017 году производство товарной продукции Удачнинским ГОК составило 3,8 млн карат. В 2018 году планируется добыть почти 5,3 млн карат, в денежном эквиваленте − 510,5 млн долларов США.
Город Удачный, 2017 год
Город Удачный, 2017 год
Подземный рудник
Погрузочно-доставочная машина отгружает руду
Дорога на Муну
Закрытие карьера Удачный, 2015 год
Наземный комплекс подземного рудника
Буровой станок в подземном руднике
А.Ф. Махрачёв
Обогатительная фабрика №12
ОСНОВНЫЕ ЦЕХА УГОК:
Подземный рудник «Удачный» им. Ф.Б. Андреева
Самый крупный по производительности, в настоящее время считается флагманом подземной добычи Компании. Добыча алмазов открытым способом началась в 1967 году и завершилась в 2015. Сейчас разработка месторождения идет подземным способом. Первая очередь подземного рудника введена в эксплуатацию в 2014 году. При строительстве и эксплуатации применяются передовые проектные, инженерно-технические и технологические решения, современная техника и оборудование отечественного и импортного производства. Объем добычи алмазов в 2017 году составил 1614,4 тыс. карат.
Карьер «Зарница»
Кимберлитовая трубка «Зарница», была открыта в 1954 году и стала первым коренным месторождением алмазов в Советском Союзе. Разработка трубки долго откладывалась, так как содержание алмазов в ней ниже, чем на других месторождениях. В небольших объемах работы на «Зарнице» начались в 1998 году, до настоящего времени на трубке добывали порядка 1 млн. тонн руды в год. На протяжении трех лет ведется работа по снижению себестоимости алмазодобычи, применяются новые методы транспортировки, которые позволили повысить рентабельность разработки данного месторождения. В 2017 году объем добычи руды составил 2 млн 602 тыс. тонн. Объем добычи алмазов — 785,6 тысяч карат. Согласно долгосрочной программе горных работ, на месторождении «Зарница» ежегодно будут добывать 3,5 млн тонны руды.
Россыпные месторождения: «Законтурная делювиальная россыпь трубки «Удачная» и «Пироповый ручей»
Россыпные месторождения имеют небольшие объёмы, и отработка месторождений запланирована с 2014 по 2019 год. Объем добычи алмазов в 2017 году составил 294,8 тысяч карат.
Месторождение «Верхне-Мунское»
С 1 июля в составе Удачнинского ГОК начал функционировать горнодобывающий комплекс «Верхне-Мунский», расположенный на расстоянии 170 км от города Удачного.
В сентября 2018 планируется завершение строительства и начало добычи алмазов на кимберлитовых трубках этого рудного поля.
Отработку планируется вести двумя карьерами: «Заполярный» (трубки «Заполярная» и «Деймос») и «Магнитный» (трубки «Комсомольская-Магнитная» и «Новинка»). Добытую руду будут перевозить автопоездами с грузоподъемностью 95 тонн для извлечения алмазов на фабрику №12. Проектная мощность предприятия – 3 млн. тонн руды в год.
Обогащение руды
Руда со всех месторождений Удачнинского ГОК обрабатывается на обогатительной фабрике №12. Первая очередь фабрики введена в строй 1976 году. В настоящий момент фабрика проходит техническое перевооружение – на ней будет внедрено новое энергоэффективное оборудование, которое позволит повысить технологические параметры обогащения и в 2019 году выйти на проектную производительность 10,5 млн тонн руды. С 2018 года началось строительство нового участка оборотного водоснабжения, сгущения, транспортировки и складирования отвальных продуктов. Реализация данного проекта позволит существенно снизить расходы на обогащение и складирование хвостов обогащения.
Последнее обновление страницы было сделано 03 сентября 2013 в 10.14
Горное дело | Britannica
Добыча , процесс добычи полезных ископаемых с поверхности Земли, включая моря. Минерал, за некоторыми исключениями, представляет собой встречающееся в природе неорганическое вещество, которое имеет определенный химический состав и отличительные физические свойства или молекулярную структуру. (Одно органическое вещество, уголь, также часто рассматривается как минерал.) Руда — это металлосодержащий минерал или совокупность металлосодержащих минералов и пустой породы (связанной породы, не имеющей экономической ценности), которую можно добывать с прибылью. Месторождение полезных ископаемых обозначает естественное проявление полезного минерала, а месторождение руды обозначает месторождение полезных ископаемых достаточной площади и концентрации, чтобы можно было начать разработку.
Типовые разработки подземных выработок. Encyclopædia Britannica, Inc.При оценке месторождений полезных ископаемых чрезвычайно важно помнить о прибыли. Общее количество полезных ископаемых в данном месторождении называется запасами полезных ископаемых, но только то количество, которое может быть добыто с прибылью, называется запасами руды .По мере роста продажной цены минерала или снижения затрат на добычу доля запасов полезных ископаемых, классифицируемых как руда, увеличивается. Очевидно, что верно и обратное, и рудник может прекратить добычу, потому что (1) минерал исчерпан или (2) цены упали или стоимость выросла настолько, что то, что когда-то было рудой, теперь стало только минералом.
История
Археологические находки указывают на то, что добыча полезных ископаемых велась еще в доисторические времена. По-видимому, первым использованным минералом был кремень, который из-за своей раковинной трещиноватости можно было разбить на части с острыми краями, которые использовались в качестве скребков, ножей и наконечников стрел.В период неолита, или нового каменного века (около 8000–2000 до н.э.), шахты глубиной до 100 метров (330 футов) были погружены в отложения мягкого мела во Франции и Великобритании, чтобы извлечь найденную там кремневую гальку. Другие минералы, такие как красная охра и медный минерал малахит, использовались в качестве пигментов. Самая старая известная подземная шахта в мире была затоплена более 40 000 лет назад на хребте Бомву в горах Нгвенья, Свазиленд, для добычи охры, используемой в церемониях захоронения и в качестве окраски тела.
Золото было одним из первых использованных металлов, его добывали в руслах из песка и гравия, где оно возникло как чистый металл из-за его химической стабильности. Хотя химически медь менее стабильна, она существует в самородной форме и, вероятно, была вторым металлом, обнаруженным и использованным. Серебро также было найдено в чистом виде и когда-то ценилось выше золота.
Получите эксклюзивный доступ к контенту из нашего 1768 First Edition с подпиской. Подпишитесь сегодняСогласно историкам, египтяне добывали медь на Синайском полуострове еще в 3000 г. до н. Э., Хотя часть бронзы (медь, легированная оловом) датируется 3700 г. до н. Э.Железо датируется 2800 годом до нашей эры; Египетские записи о плавке железной руды датируются 1300 годом до нашей эры. Свинец, найденный в древних руинах Трои, производился еще в 2500 году до нашей эры.
Одним из самых ранних свидетельств строительства из камня было строительство (2600 г. до н.э.) великих пирамид в Египте, самая большая из которых (Хуфу) имеет длину 236 метров (775 футов) по сторонам основания и содержит примерно 2,3 миллиона блоков два вида известняка и красный гранит. Считается, что известняк добывали на другом берегу Нила.Блоки весом до 15 000 кг (33 000 фунтов) были транспортированы на большие расстояния и подняты на место, и они демонстрируют точную резку, которая привела к точной подгонке кладки.
Одно из наиболее полных ранних описаний методов добычи полезных ископаемых в Европе было сделано немецким ученым Георгиусом Агриколой в его De re Metallica (1556). Он подробно описывает методы проходки валов и туннелей. Мягкую руду и породу кропотливо добывали киркой, а более твердую — киркой и молотком, клиньями или жаром (установка огня).При поджоге у скалы сложили кучу бревен и сожгли их. Тепло ослабляет или разрушает породу из-за теплового расширения или других процессов, в зависимости от типа породы и руды. При необходимости использовались грубые системы вентиляции и откачки. Подъем валов и подъемов производился брашпилем; перевозки осуществлялись в «грузовиках» и тачках. В туннелях использовались системы деревянных опор.
Большой прогресс в добыче полезных ископаемых был достигнут, когда секрет черного пороха достиг Запада, вероятно, из Китая в позднем средневековье.В середине 19 века его заменили в качестве взрывчатого вещества динамитом, а с 1956 года широкое распространение получили горючие взрывчатые вещества и шламы из нитрата аммония (смеси воды, топлива и окислителей). Стальное сверло с острием клина и молоток сначала использовались для просверливания отверстий для размещения взрывчатых веществ, которые затем загружались в отверстия и взрывались для разрушения породы. Опыт показал, что правильное размещение скважин и порядок стрельбы важны для получения максимального дробления горных пород в шахтах.
Изобретение механических буров, приводимых в действие сжатым воздухом (пневматические молоты), значительно увеличило возможности разработки твердых горных пород, в несколько раз снизив стоимость и время земляных работ. Сообщается, что англичанин Ричард Тревитик изобрел роторную дрель с паровым приводом в 1813 году. Механические поршневые сверла, в которых использовались насадки на буровых штангах и двигались вверх и вниз, как поршень в цилиндре, датируются 1843 годом. были изобретены современные воздушные дрели.На смену поршневым сверлам пришли перфораторы, работающие на сжатом воздухе, и их производительность улучшилась благодаря улучшенной конструкции и доступности качественной стали.
Развитие бурения сопровождалось усовершенствованием методов погрузки, от ручной погрузки лопатой до различных типов механических погрузчиков. Транспортные перевозки также превратились из перевозки людей и животных в шахтные вагоны, запряженные электровозами и конвейерами, и в транспортные средства большой вместимости с резиновыми шинами. Аналогичные изменения произошли в открытых горных разработках, что привело к увеличению объемов производства и значительному снижению стоимости металлических и неметаллических продуктов.Большие вскрышные машины с землеройными колесами, применяемые при открытой добыче угля, применяются в других типах карьеров.
Приток воды был очень важной проблемой при подземной добыче полезных ископаемых, пока Джеймс Ватт не изобрел паровой двигатель в 18 веке. После этого паровые насосы можно было использовать для удаления воды из глубоких шахт. Ранние системы освещения были типа открытого пламени, состоящие из свечей или масляных ламп. В последнем случае сжигали уголь, китовый жир или керосин.Начиная с 1890-х годов горючий газ ацетилен генерировался путем добавления воды к карбиду кальция в основании лампы, а затем выпускался через струю в центре яркого металлического отражателя. Кремневый искровый газ позволял легко зажигать эти так называемые карбидные лампы. В 1930-е годы цокольные лампы с батарейным питанием начали применяться в шахтах, и с тех пор были внесены различные улучшения в интенсивность света, срок службы батарей и вес.
Несмотря на то, что вокруг майнеров и горнодобывающих предприятий накопилось много мифов и романтических историй, в современной горнодобывающей промышленности именно машины обеспечивают силу, а обученные майнеры дают мозги, необходимые для победы в этой высококонкурентной отрасли.Технологии развиваются до такой степени, что золото теперь добывается под землей на глубине 4000 метров (около 13 100 футов), а самые глубокие открытые рудники вырываются на глубину более 700 метров (около 2300 футов).
Джордж Б. Кларк Уильям Эндрю Хуструлид.Как работает подземная горная промышленность | HowStuffWorks
Есть подземные рудники с твердыми породами и есть подземные рудники с мягкими породами. Например, угольные месторождения обитают в относительно мягких осадочных породах. Золотые месторождения обитают в вулканических или метаморфических породах, которые являются относительно твердыми, как и алмазы, медь, серебро, никель и цинк [источник: Great Mining].
Даже внутри категории твердых пород методы проектирования и добычи различаются, но почти все они основаны на нескольких основных методах:
Помещение и столб — Для относительно плоских рудных залежей с небольшим изменением высоты по всей высоте горняки пробуривают пандус доступа к залежи и удаляют руду в виде ям (комнат) и опор (столбов) крыши.Помещения могут быть добыты с использованием обычных зарядно-взрывных технологий или, что сейчас чаще, с помощью машины, называемой комбайном непрерывного действия . Горняк непрерывного действия бурит горную породу до тех пор, пока она не образует выкопанную комнату, примерно от 20 до 30 футов (от 6 до 9 метров), оставляя на месте каменный столб для поддержки «крыши» [источник: United Mine Workers of America]. Машина перемещается по руде, создавая комнаты и столбы, пока не будет покрыто все месторождение. Последний проход сверлит колонны для извлечения руды, позволяя крышам обрушиться за машиной, когда она покидает каждую комнату.
Cut and Fill — Для относительно узких рудных залежей горняки буриют подъездную эстакаду, прилегающую к залежи руды, от поверхности до самой нижней точки месторождения. Затем оператор пропускает бур через руду, создавая штрек или горизонтальный проход от одной стороны месторождения к другой. В самых твердых породах опора крыши не требуется; в более мягких породах болты могут быть помещены в кровлю по мере выполнения бурения [источник: ноу-хау в горнодобывающей промышленности].После завершения проходки засыпка или отходы распределяются в открытый проход, создавая платформу для следующего прохода. Буровая установка перемещается поверх этой засыпки, чтобы прорезать еще один проход через руду. Это продолжается до тех пор, пока буровая установка не прорежет верхнюю часть залежи руды.
Этот метод также может быть использован на более широких месторождениях, путем бурения двух смежных съездов и прорезания двух соседних выработок, часто называемых выемками и заполнением [источники: ноу-хау в горнодобывающей промышленности].
Cut and fill предназначен для твердых пород, так как он не имеет опорных механизмов, присущих и центральных для такого метода, как комната и столб. С другой стороны, подход «комната и колонна» легко проникает в более мягкие материалы — и в большинство угольных шахт.
,Строительство подземных рудников | Статья о подземном строительстве шахт по The Free Dictionary
строительство предприятий, таких как угольные и рудные шахты, для подземной добычи полезных ископаемых. Строительство подземных горных выработок включает рытье вертикальных, наклонных и горизонтальных подземных горных выработок и возведение зданий и сооружений на поверхности. Поверхностные конструкции и здания включают в себя головные рамы, здания подъемных машин, здания, используемые как для административных, так и для общих служебных целей, мастерские по ремонту машин, градирни, компрессорные отделения, склады и подъездные пути.При подземном строительстве шахт более 60 процентов от общего объема строительно-монтажных работ выполняется под землей.
В дореволюционной России подземные шахты строились в основном в Донецком угольном бассейне (Донбасс) и Криворожском железорудном бассейне. В СССР подземное шахтостроение бурно развивалось в предвоенные пятилетки (1929–40). Крупные подземные угольные шахты были построены на Донбассе, в Кузнецком угольном бассейне (Кузбасс) и в Караганде в Казахстане.Подземные рудники были построены, например, в Криворожском бассейне и Пермской области.
В годы Великой Отечественной войны 1941–45 активизировалось строительство подземных рудников в восточных районах СССР. Только в Кузбассе за годы войны было введено в строй 24 шахты.
В период с 1943 по 1950 год основная часть работ по строительству подземных рудников была посвящена реконструкции разрушенных или затопленных шахт на Донбассе, Московском угольном бассейне, Криворожском бассейне и Никопольском марганцеворудном бассейне.
Дальнейшее развитие строительства подземных рудников характеризовалось большей опорой на специализированное оборудование и совершенствованием организационных форм управления. Между 1950 и концом 1970-х годов в СССР строились или строились многочисленные подземные рудники. В их числе угольные шахты (такие как шахта Распадская № 1 на Кузбассе, шахта Красноармейск-Капитальная на Донбассе, шахта Ворга-Шор № 1 в Печорском угольном бассейне), калийно-соляные шахты (например, обслуживающие Четвертый Березниковский калийный комбинат на Урале и Четвертый Солигорский калийный комбинат в Белоруссии), а также железные рудники (такие как Октябрьско-Саксаганский и Гигант-Глубокский рудники в Криворожском бассейне и рудник Яковлево в Курске. Магнитная аномалия).
Подземные шахты, как правило, строятся в сложных горно-геологических условиях на глубинах до 1000 и более метров. Такие глубины характеризуются высокими температурами вмещающих пород, повышенным горным давлением и газовыделением. Значительный объем земляных работ проводится для обновления существующих подземных рудников и подготовки новых уровней в таких рудниках.
Проходка стволов полностью механизирована. Буровые установки БУКС-лм используются для бурения взрывных скважин.Для погрузки насыпной породы используются погрузочные машины, а для доставки породы на поверхность используются мощные саморазгружающиеся ковши вместимостью до 5 м. 3 . Стволы обычно армируют монолитным бетоном путем заливки бетонной смеси по трубам за подвижной металлической опалубкой.
Для ввода в эксплуатацию современного подземного рудника от 40 до 80 км горных выработок. Ежегодно строители выкапывают более 360 км горных выработок, в том числе 25 км вертикальных стволов.В 1976 г. средняя скорость проходки ствола с применением горно-погрузочных комплексов составляла 55 м / мес. В угольной промышленности и 43,6 м / мес. В горнорудной промышленности. СССР занимает первое место в мире как по объему, так и по скорости проходки вертикальных стволов; Всего за месяц прокладывается 401,3 м готовых стволов. Для проведения горизонтальных выработок используются буровые установки, горно-погрузочные машины и проходческие машины. В 1975 г. около 15% всех выработок подземных шахт, построенных угольной промышленностью, было выполнено с помощью режущих машин; около 20 процентов всех таких раскопок, то есть 1.В 5 раз больше планового — выполнено скоростной техникой. В 1976 г. среднемесячная норма выемки грунта составляла 59,7 м выемок и штреков на угольных шахтах и 69,6 м на рудниках. Объем грунта, удаляемого за месяц при выработке котлованов большого сечения, например, днищ котлованов и камер, составляет от 300 до 460 м 3 .
Подземные рудники строятся горно-строительными организациями, специализирующимися на выполняемых работах. К организациям относятся тресты, которые осуществляют прокладку шахт, проводят горизонтальные или наклонные котлованы, устанавливают горное оборудование или возводят здания и сооружения на поверхности.Такие организации принадлежат горно-строительным комбинатам или объединениям, например, Всесоюзному объединению «Союзшахтстрой» Министерства угольной промышленности СССР и Всесоюзному объединению «Цветметшахтстрой» Министерства цветной металлургии СССР. Специализированный Всесоюзный трест «Шахтспецстрой» Министерства строительно-монтажных и специальных строительных работ СССР осуществляет прокладку шахт специальными методами, например, замораживанием или заливкой горных пород.
Научные исследования по подземному горному строительству проводят такие НИИ, как Всесоюзный научно-исследовательский институт организации и механизации подземного горного строительства (Харьков), Кузбасский научно-исследовательский институт подземного горного строительства (Кемерово) и Донецкий государственный институт планирования и организации подземного строительства шахт (Донецк).Режущие машины разработаны Центральным научно-исследовательским институтом подземного горного машиностроения в Москве.
В других социалистических странах были построены крупные подземные угольные шахты в Польской Народной Республике, подземные калийно-солевые шахты в Германской Демократической Республике, а также большие подземные шахты для добычи сложных руд строятся в Монгольской Народная Республика. В рамках Совета экономической взаимопомощи (СЭВ) созданы научно-технические советы по планированию и строительству горнодобывающих предприятий.
В капиталистических странах, в том числе в США, ФРГ, Бельгии, Великобритании, Франции, ЮАР, Канаде, подземные рудники строятся, как правило, специализированными фирмами.
СПИСОК ЛИТЕРАТУРЫ
Строительство зданий и сооружений угольных шахт . Москва, 1964.Новая технология строительства шахтных стволов . Москва, 1965.
«Шахтное строительство за годы Советской власти». Шахтное строительство , 1967, №1.10.
Гузеев А.Г. Основы проектирования технологий строительства и реконструкции шахт . Москва, 1972.
Справочник инженера-шахтостроителя , тт. 1-2. Москва, 1972.
Машины и оборудование для проведения горизонтальных и наклонных горных выработок . М., 1975.
Малиованов Д.И. «Современные тенденции в совершенствовании горнопроходческого оборудования». Шахтное строительство , 1976 г., № 2-3.
Проектирование угловых шахт .Москва, 1976..